It’s nice to see the autonomous tuggers work within the operation seamlessly alongside humans.
TREY CURTAIN
Industrial Engineer, FedEx Ground, Greensboro, NC.
Rise in non-conveyables slows productivity
FedEx Ground processes nine million packages a day across its 39 North American hubs. With the rise of e-commerce making it possible to buy just about anything online, ten percent of those packages are non-conveyable or oversized shipments. That’s 900,000 shipments of things like car engines, kayaks, and recliners. All too big for traditional sortation systems—contributing to significant logistical challenges.
The team at the FedEx Ground hub in Greensboro, NC, sought a better way to handle non-conveyables. They reassigned employees to manually process and transport shipments throughout the hub using traditional tuggers as a stop-gap measure. This approach drained productivity and created bottlenecks across the entire operation.
Time for an autonomous solution
A manual process wasn’t a viable long-term solution. The Greensboro team tested Automatic Guided Vehicles (AGVs) and Autonomous Mobile Robots (AMRs) from several vendors.
Their evaluation criteria were to find a solution that would reduce the time employees spent manually driving tractors within the facility and provide a solution for non-conveyable transport to keep conveyors moving. The Greensboro site is also a highly dynamic environment, so any solution needed to safely and efficiently navigate that.
The Greensboro team ultimately selected Vecna Robotics’ high capacity AMRs for their high uptime and ability to adapt to new route assignments and changing environments in real-time with the most advanced navigation system in the industry.
As a result, the Greensboro team processed 30% more in non-conveyable volume and identified 20% more workflow improvement through analytics.
A tugger that pulls its weight
Vecna’s self-driving Autonomous Tuggers free up employees from driving tuggers with tow carts, getting on and off the vehicle repeatedly to load and unload shipments, and waiting in queue before the next task. Instead, with the new self-driving vehicles in place, employees station themselves at a load and unload point to handle the packages and focus on tasks like labeling, validation, staging, error handling, and more.
Vecna Robotics takes a flexible approach and has superior technology. Our work together represents a true partnership.
TED DENGEL
Managing Director, Operations Technology and Innovation
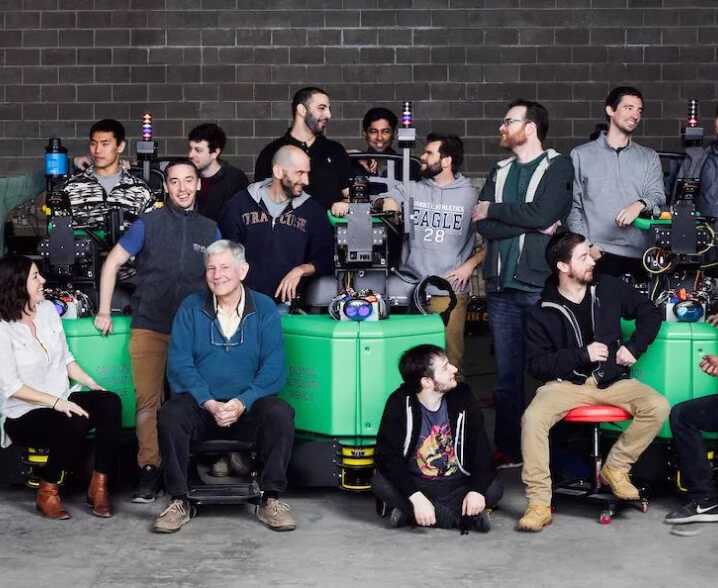
Let’s keep things moving
Connect with us. We’re just humans who love to talk about robots and how we can make your business go.