Warehouse automation trends today are being driven by the need to enhance efficiency, productivity, and cost-effectiveness while navigating complex macroeconomic and microenvironmental challenges.
Macro trends, such as the rapid growth of e-commerce, have forced warehouses to meet escalating demands for accelerated order processing and delivery. Factors like reshoring/nearshoring, supply chain disruptions, and the broader push for digital transformation within the supply chain ecosystem. Read more about how automation can help mitigate those specific trends here.
At a micro level, warehouse managers grapple with the realities of a workforce in flux. Labor shortages are compounded by escalating wages, accentuating the cost implications of human-centric operations. The potential for human-induced errors in repetitive, high-pressure tasks is another driving force. In a consumer landscape where reputation hinges on accuracy and reliability, these errors are more than financial setbacks; they can irrevocably damage a brand. Thus, the transition toward automation emerges not merely as a trend but as a strategic necessity for warehouses navigating the complexities of the modern business landscape.
Amid the rapid pace of 2023, the demand for seamless, precise, and efficient supply chain operations is unprecedented. Warehouses, as pivotal nodes within these intricate networks, are experiencing a profound transformation powered by innovative technologies and strategic paradigms. The juggernaut of e-commerce necessitates swift turnarounds and precise handling, while global uncertainties urge the exploration of localized supply chain strategies. This digital metamorphosis isn’t merely an option but a fundamental strategy to thrive in an increasingly competitive market.
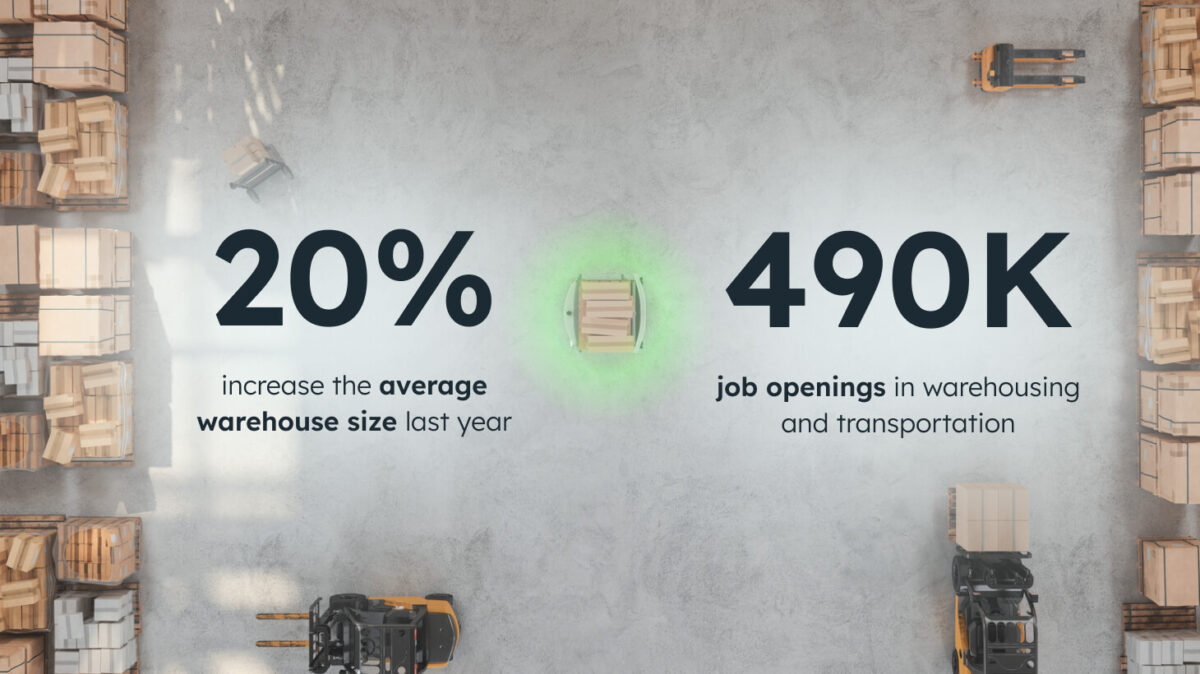
The need for real-time data and analytics has become a significant driver for warehouse automation in recent years. The dynamics of the modern supply chain demand quick decision-making and having access to real-time data is fundamental to this. IoT devices and other technologies can be used to gather data about warehouse operations and provide real-time information about inventory levels, order status, and other key metrics. And advances in technology, such as robotics and artificial intelligence, are also driving warehouse automation. The increasing capabilities of these technologies, combined with the decreasing costs, are making it more feasible for warehouses to implement automation solutions.
Amidst all of these factors pushing warehouses to innovate, here are the top 10 warehouse automation trends we see shaping 2023:
- Robotics and automation: The prevalence of robotics and automation within warehouses is on the rise, presenting a compelling solution to bolster efficiency and productivity. Notably, the Robotics Industries Association (RIA) highlighted the momentum in this direction, revealing that non-automotive robot orders in North America surged in the first quarter of 2021. A remarkable 9,972 robots, valued at $485 million, were ordered—a notable 19.6% increase in units compared to the same period in 2020, and a 3.5% increase in value. These numbers show the growing need for robotics and automation to optimize warehouse operations, with applications ranging from picking and packing to the control and monitoring of diverse processes.
In 2023, the role of robotics and automation remains central in shaping the trajectory of warehouse automation trends. The explosive growth of e-commerce and the heightened demand for expedited, streamlined deliveries have propelled warehouses to integrate robots for operational enhancement.
As technological advancements continue to unfold, robotics and automation are poised to redefine the very essence of warehouse operations. This redefinition hinges on the core tenets of speed, accuracy, and adaptability. Collectively, the surge of interest in robotics and automation is reshaping warehouse landscapes, forging a path toward elevated performance and ushering in an era where human and machine collaboration converges seamlessly. - Artificial intelligence and machine learning: In 2023, the integration of AI (Artificial Intelligence) and ML (Machine Learning) into warehouse operations emerges as a pivotal trend. These technologies are significantly enhancing efficiency, accuracy, and overall warehouse performance. AI and ML algorithms, sophisticated in their design, are now applied to diverse warehouse tasks ranging from inventory management to order fulfillment and even predictive maintenance. For instance, AI-enabled robots are equipped with visual recognition and natural language processing capabilities, allowing them to proficiently locate and pick items from shelves. Meanwhile, ML-driven algorithms can swiftly analyze vast amounts of data from sensors and IoT (Internet of Things) devices. This data-driven approach not only optimizes inventory levels but also anticipates and prevents equipment downtime, ensuring smooth and continuous operations. The fusion of these technologies heralds a new era of warehouse management where decision-making is faster, more informed, and adaptive to real-time demands.
- Internet of Things (IoT): The Internet of Things (IoT) is not merely a tech buzzword but a transformative force in warehouse operations. As warehouses strive for heightened efficiency and precision, IoT emerges as the linchpin by facilitating real-time monitoring and analysis, thanks to a network of sensors and interconnected devices.
These IoT devices offer a plethora of functions, from meticulous inventory tracking to vigilant equipment performance oversight and even refining energy consumption. The continuous stream of data these devices churn out provides a treasure trove of actionable insights. Warehouse managers, equipped with this data, are better poised to discern operational nuances, spotlight inefficiencies, and shape strategies rooted in empirical evidence. Furthermore, the predictive prowess of IoT means potential pitfalls, like equipment failures, are flagged in advance. This proactive approach translates to minimized operational interruptions and a tangible reduction in unexpected maintenance expenditures, ensuring a smoother, more cost-effective workflow. - Automated guided vehicles (AGVs): The AGV market is growing at a rapid rate. With projections indicating its growth from a formidable USD 2.2 billion in 2021 to an impressive USD 3.2 billion in 2026, AGVs are fast becoming the backbone of contemporary warehousing. These vehicles, acting as the silent orchestrators, ensure seamless transportation of materials within the confines of warehouses and distribution centers, bridging the gap between various zones, facilitating pick-and-place operations, and even shouldering the responsibility of loading and unloading vehicles.
Integral to their design, AGVs come fortified with an array of sensors and advanced navigation systems. These features empower AGVs to chart their course with finesse, evading obstacles, and ensuring the sanctity of their environment. Beyond the obvious operational benefits, the integration of AGVs translates to palpable financial advantages — from curtailing labor expenses to bolstering operational throughput. Furthermore, the strategic deployment of AGVs ensures that mundane, repetitive tasks are efficiently managed, allowing the human workforce to channel their energies towards tasks that demand cognitive prowess and critical thinking, thus marrying efficiency with innovation. - Voice picking: Voice picking is a technology steadily gaining traction for its pragmatic benefits. This avant-garde system equips warehouse operatives with the power of voice, allowing them to seamlessly engage with wireless headsets and converse through voice prompts. In essence, it transforms the erstwhile paper-dependent picking lists or handheld device methodologies into relics of the past.
Powered by sophisticated speech recognition mechanisms, this technology meticulously deciphers voice instructions, offering instantaneous feedback and validation. Research and practical applications underline the efficacy of voice picking in augmenting picking precision, slashing errors, and turbocharging overall productivity. A salient advantage, often underscored, is the ergonomic nature of voice picking. With hands unburdened by devices or papers, workers sidestep the pitfalls of repetitive stress injuries, emphasizing workplace well-being. To add another layer of operational sophistication, voice picking isn’t an isolated entity. It’s been designed for seamless integration with Warehouse Management Systems (WMS), ensuring real-time inventory assessments and elevating the accuracy quotient of order fulfillment processes. Thus, voice picking emerges as a holistic solution, harmonizing efficiency with worker safety. - Autonomous mobile robots (AMRs): Within the contemporary warehousing landscape, Autonomous Mobile Robots (AMRs) are becoming game-changers. Their ascendancy is rooted in their unmatched capability to seamlessly ferry goods and raw materials throughout the vast expanse of warehouse floors. But, their prowess isn’t confined to mere transportation. These sophisticated robots are embedded with advanced navigation systems, enabling them to chart intricate paths while effortlessly circumventing impediments and averting potential collisions. These feats are underpinned by stringent safety protocols that these robots adhere to, ensuring a harmonious coexistence with the human workforce.
Yet, the marvels of AMRs don’t end with their physical attributes. Their technological integration extends into the digital realm, with most modern AMRs being cloud-enabled. This connectivity introduces a plethora of advantages: dynamic performance enhancements become feasible, routine software maintenance becomes a breeze, and granular performance metrics can be analyzed in real-time. Thus, beyond their immediate operational contributions, AMRs open the doors to insights and adaptability, playing a pivotal role in the evolving warehouse ecosystem. Their ascent signifies the fusion of physical dexterity with digital intelligence, setting the tone for the warehouses of the future. - Blockchain: Blockchain technology is increasingly being explored as a way to improve transparency, traceability, and security in warehouse operations. At its core, blockchain offers a reliable, chronological database that is decentralized and transparent. This ensures that every transaction or movement within the warehouse is not only recorded but also verifiable by all parties involved, eliminating any chances of double-spending or false reporting. By recording every touchpoint—from the entry of a product into the warehouse to its final shipment—blockchain negates the grey areas that lead to inefficiencies or disputes.
It also fosters a new level of collaboration among stakeholders. Given that the ledger is shared, every entity in the supply chain, be it the raw material provider or the end retailer, can access real-time data about inventory status, fostering trust and enabling proactive decision-making. This revolutionary approach ensures a synergy rarely seen before in warehousing operations. As blockchain’s adoption accelerates, it’s poised to redefine not just the mechanics, but the ethos of warehouse management, prioritizing transparency, trust, and collaboration above all. - Augmented reality (AR): The advent of Augmented Reality (AR) in warehousing signifies a transformative step in the way operations and training processes are conducted. AR glasses or headsets superimpose digital information onto the physical world, streamlining operations and minimizing disruptions. When a worker, for instance, is on a pick task, they don’t have to rely on memory or constantly refer to a handheld device. Instead, AR provides an unintrusive guidance system, directing them seamlessly. This is especially crucial during peak periods or during stocktaking activities, where precision and speed are of the essence.
There’s also the reality of the workforce demographic shifting to younger, tech-savvy individuals coming on board and adopting such technologies ensures that the learning curve is shortened. The visual, interactive nature of AR resonates with the digital native generation, making onboarding smoother. Moreover, when machinery malfunctions or needs routine maintenance, AR assists workers by giving them a virtual, step-by-step guide, reducing downtimes and ensuring adherence to best practices. In essence, AR acts as an intuitive bridge between the digital and physical, enhancing warehousing operations manifold. - Cloud computing: Cloud computing is emerging as a cornerstone of modern warehousing solutions. Moving away from the limitations of traditional, on-premises IT infrastructure, cloud platforms offer unmatched agility, allowing warehouses to quickly adapt to changing market conditions and customer demands. The ability to scale resources on-demand, both up and down, ensures operational efficiency without the need for heavy upfront investments.
Beyond just financial advantages, utilizing the cloud fosters collaboration. By centralizing data, teams across different locations can access unified, up-to-date information, promoting more coordinated efforts. Moreover, cloud providers invest heavily in security measures, offering businesses robust protection against cyber threats. Furthermore, software updates become seamless, ensuring warehouses are always leveraging the latest technology innovations. As integration capabilities improve, marrying cloud platforms with other cutting-edge technologies like AI and analytics will only further optimize warehouse processes, driving more informed, data-driven strategies. - 3D printing: As global supply chains face increasing complexities and challenges, 3D printing is becoming more and more of a reality within warehouse operations. By having the capability to create parts on-demand, warehouses can significantly diminish their dependence on external suppliers and avoid potential disruptions or delays. Furthermore, this on-site production approach reduces the need for large storage spaces dedicated to spare parts inventory, optimizing space utilization and management.
Additionally, as industries lean towards personalization, 3D printing allows warehouses to meet these tailored demands without necessitating large-scale production runs. In the long run, this can lead to reduced carbon footprints, as less transportation of parts is required. As advancements in 3D printing technology continue, the materials and processes will become even more cost-effective and environmentally friendly, amplifying its significance in the modern warehouse setup. As businesses recognize these advantages, adoption is set to increase, positioning 3D printing as a fundamental tool in future-proofing warehouse operations.
Overall, these trends are aimed at increasing efficiency, reducing human error, and automating repetitive tasks within warehouse operations. This drive for improvement is being powered by the integration of cutting-edge technologies such as the Internet of Things (IoT) and Artificial Intelligence (AI). These technologies empower warehouses to collect, analyze, and act upon data, subsequently elevating the overall performance of the facility. Moreover, the proliferation of innovations like autonomous mobile robots, voice-based picking systems, and Automated Guided Vehicles (AGVs) is reshaping the labor landscape by minimizing human intervention and amplifying productivity.
Emerging technologies such as Augmented Reality (AR), blockchain, and 3D printing are imparting a new level of customization and adaptability to warehouse processes. This infusion of diverse technologies is driven by a shared motivation: the mounting consumer demand for swifter deliveries, real-time order tracking, and unwavering precision. Within an increasingly competitive global market, warehouses are navigating a delicate balance between impeccable service and cost containment. In this pursuit, contemporary solutions like cloud computing not only address these challenges but also furnish scalability to accommodate future growth, ensuring warehouses remain resilient against surges in demand.
Looking beyond the warehouse, these technological advancements resonate within a broader context—the larger narrative of digital transformation sweeping across industries. Warehouse management is but a single facet of a comprehensive supply chain revolution. As technology evolves at an unprecedented pace, conventional warehouse boundaries are expanding, giving rise to an interconnected, adaptive system capable of navigating the dynamic currents of the market. In essence, the warehouse of the future transcends being a mere repository; it evolves into an epicenter of innovation, efficiency, and flexibility, all underpinned by the rapid march of technological progress.
Vecna Robotics has a wide range of pallet handling solutions that can guide your warehouse automation transformation journey right away. For more information about how you can get started, go to our From No Bot to Robot page, or contact us today to schedule a consultation with a factory automation expert.