As the warehousing industry grows and changes, warehouse CEOs and executives must keep up with advancing technology. Automated forklifts utilizing AGV (Automated Guided Vehicle) and AMR (Autonomous Mobile Robot) technology can revolutionize a warehouse’s efficiency and give your business an edge in an increasingly competitive field. By automating some of the more tedious labor-intensive processes, these vehicles make warehouses faster, safer, and smarter—not to mention more profitable.
In this blog post, we will explore how automated forklifts work by looking at Frequently Asked Questions.
1. What are automated forklifts and AGV forklifts?
Automated forklifts are extremely versatile machines that can be used in a variety of transportation applications within factories, warehouses, and distribution and fulfillment centers. Also known as AGV or AMR forklifts, these vehicles are specialized pieces of machinery used for lifting and moving heavy objects or materials without the need for a human pilot. They are equipped with sensors and a guidance system to ensure precise movements and eliminate the need for manual labor. The machines can be programmed to move in any direction, run at different speeds, and adjust their route based on the environment. By automating tedious tasks, they can improve efficiency and reduce costs significantly.
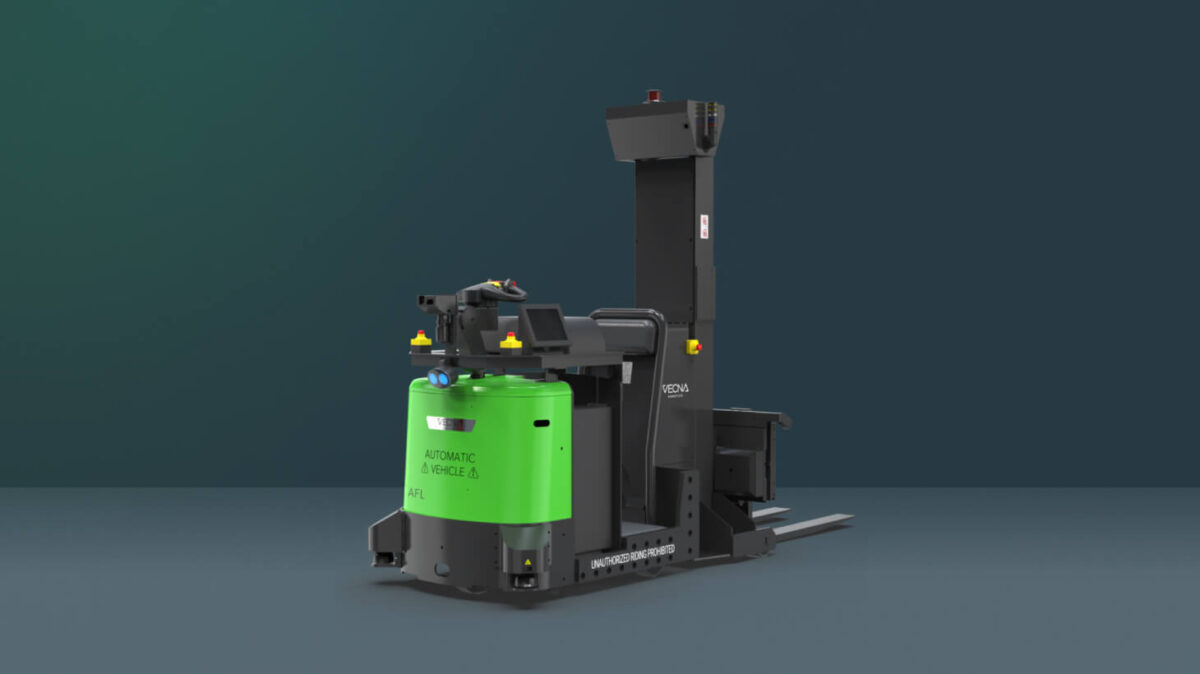
2. How do automated forklifts work?
They usually consist of a frame, electric motors, sensors, wheels, and onboard computing power. The sensors allow the vehicle to detect obstacles in its path and change course accordingly. The ability to circumvent obstructions helps ensure safety while allowing the machines to easily navigate busy factories.
3. How do automated forklifts navigate?
The automated forklift is also equipped with computer-controlled navigation systems that allow operators to assign destinations to which the vehicle will go. Once programmed, the vehicle will undertake its journey autonomously, following any turns or curved paths along its specified route with precision, avoiding obstacles as necessary.
4. What are the benefits of using automated forklifts?
The most obvious benefit is the reduction in labor costs, as these machines do not require human drivers and can be programmed to perform specific tasks. This improves efficiency and increases productivity by reducing the labor intensity of warehousing transportation.
In addition, automated forklifts are very safe to operate, as they are outfitted with sensors that detect obstacles in their path and make course corrections accordingly. Their payload never obscures their vision, and they don’t cut corners to speed things up. Furthermore, automated forklifts won’t make the mistake of trying to lift a load greater than the weight for which the truck is rated – a common error that humans make. These factors help to reduce workplace accidents due to human error.
5. How do I choose the right automated forklift for my business?
First, you’ll need to determine the size and weight capacity required for your application. This will help you narrow down your choices and find the right machine for the job.
Next, you should look into different types of automation technology available and decide which one best meets your needs. The type of automation technology you choose (AGV vs. AMR) can have a big impact on how efficiently your tasks are completed.
Finally, consider other features such special attachments and integration with your warehouse management system (WMS). You’ll want to make sure that whatever machine you select has all the components necessary for completing the tasks at hand. Additionally, it may be beneficial to research customer reviews to ensure that the automated forklifts meet all safety standards and function appropriately in terms of performance and durability.
6. How much do automated forklifts cost?
The cost of automated forklifts and AGV forklifts depends on a variety of factors, including size, weight capacity, type of automation technology, and additional features. Generally speaking, these machines cost over $100,000 for the vehicle itself, and can be much higher than that depending on the model you choose. You also need to consider the total cost of ownership (TCO) – such as installation, software, and maintenance costs – not just the vehicle itself, which can be 2-3x the cost of the vehicle. Of course, some companies like Vecna Robotics provide their robotics solutions as a service akin to how one procures software. The robots work the same but are sold for a low annual fee for a specific contracted term that typically includes all services, warranty and support, unlike a more traditional capex purchase.
7. Are there any safety concerns with using automated forklifts?
The safety concerns come from NOT automating.
Forklifts are one of the greatest hazards in the warehousing industry. OSHA estimates that on a yearly basis, forklifts cause about 85 fatal accidents and 34,900 accidents resulting in serious injury.
With rush hires and inexperienced workers handling high-stress order fulfillment, accident rates are likely to increase.
By switching to autonomous forklifts, logistics managers can keep their people safer and avoid the extremely high cost of injuries.
Conclusion
Investing in automated forklifts can greatly increase productivity and safety in warehouses, factories, or other industrial settings. By considering the size, weight capacity, type of automation technology, features, and cost associated with different machines, you can make an informed decision about which automated forklift or AGV forklift is best for your business needs.
If you have any additional questions or would like to learn more about Vecna’s selection of robots, please contact us to set up an appointment with a Vecna Robotics automation expert.