Sensing & Localization
AMR: the New AGV
Comparing AMRs and AGVs: What’s Your Best Option
For years, automated guided vehicles (AGVs) have been a mainstay in reducing non-value-added travel in the warehouse. In the face of major industry headwinds, today’s market demands the advanced flexibility, scalability, and performance of autonomous mobile robots (AMRs).
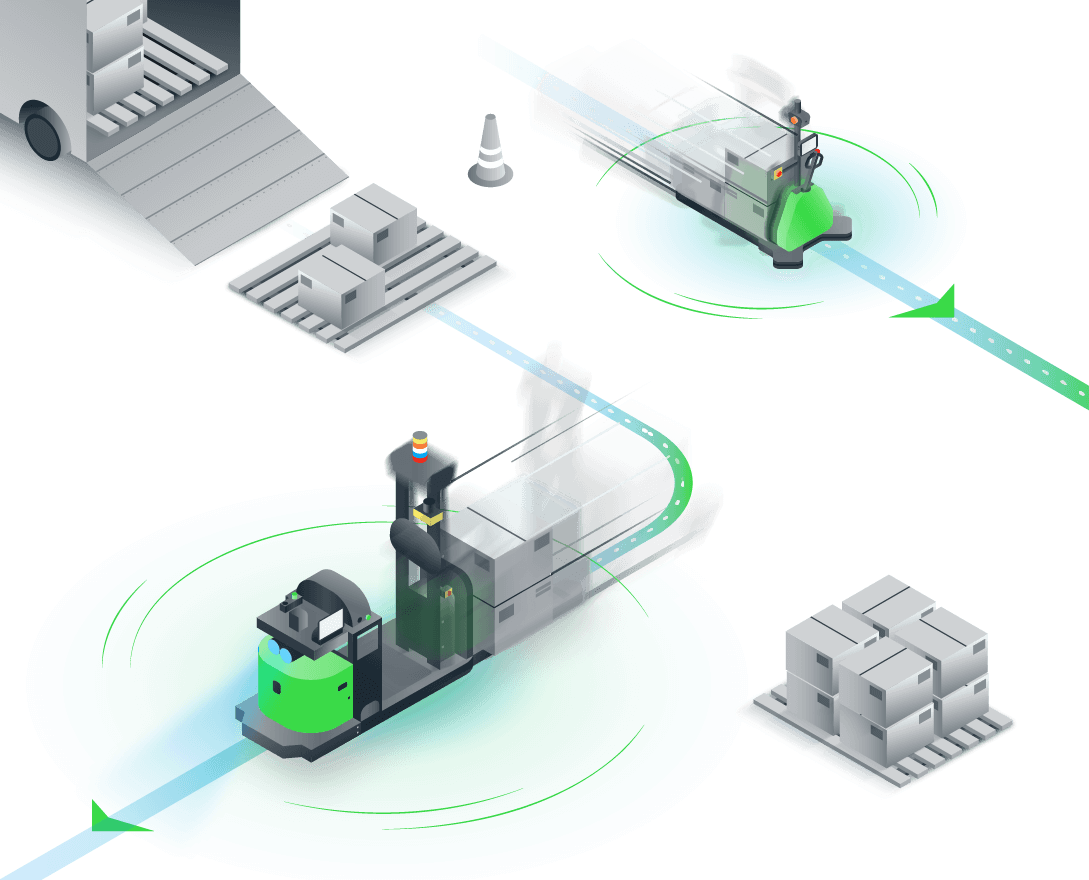
Introduction to AMRs and AGVs
Automated Guided Vehicles
AGVs are self-driving vehicles that follow pre-determined paths. They’re used primarily in manufacturing – as well as occasionally in warehousing and distribution industries – for repetitive tasks along controlled routes, such as transporting goods and materials between production lines, or moving finished products between storage or shipping areas. They are equipped with sensors to detect their environment and objects in their path, but cannot independently adjust their route or navigate obstacles.
Autonomous Mobile Robots
Autonomous Mobile Robots (AMRs) are self-driving robots that use advanced sensing and navigation technology to flexibly navigate their environment without being limited to fixed paths. They are equipped with multiple sensors – including LiDAR and cameras – that enable them to detect obstacles, people, or other objects in their environment and adjust their paths accordingly, or reroute in real-time. AMRs are well-suited for dynamic workflows and environments, such as moving goods in large warehouses or JIT routing of materials in factories.
Comparing AMR and AGV Navigation
Utilize 3D sensor fusion combining lidars, vision, and 3D perception to sense and perceive the world in realtime.
May utilize infrastructure-free sensing such as lidar or cameras, or require additional markers such as laser targets, magnets, wires etc…
Path Planning
Assesses multiple routes and dynamically plan the most efficient path to their destination, adapting and rerouting as needed.
Follow predetermined, point-to-point routes. Cannot change a chosen route or deviate from a fixed “virtual line” without intervention.
Obstacle Avoidance & Recovery
Detects obstacles and dynamically adjusts path/plots a safe route to circumvent blockages.
Stops for obstacles and cannot proceed until path is clear. May require a physical reset after a safety stop.
Payload Docking
Looks for and identifies the correct payload to move. Dynamically adjusts to staged pallets/payloads even if they are misaligned.
Docks to a predetermined location. Payloads must be precisely positioned. Requires intervention if they are staged out of spec.
Best for
Flexible and adaptive material handling tasks. AMRs are capable of updating routes in real-time and are best suited for dynamic workflows with variable demand and flexible routing, such as picking, putaway, replenishment, and sortation.
Repetitive material handling tasks. AGVs operate well in a highly structured environment with predetermined paths or routes, making them suitable for applications that require the precise and predictable movement of goods.
Summary
Actively responds to changes in the environment
Repeats pre-programmed behavior
Cost Considerations
When weighing AGVs vs. AMRs, it may be tempting to lean towards a solution with a lower price point. However, other factors impact the overall cost and the potential return on investment for your company.
AGV
While AGVs typically cost less per robot than AMRs, you must also consider the costs to set up, deploy, reconfigure, and operate them. AGVs usually require the installation of physical guides, under-floor wiring, or magnetic tape stripes to allow the AGV to navigate and locate itself in its surroundings, which comes with costly recommissioning costs. And even for infrastructure-free AGVs, these often require multiple dedicated FTEs to manage and “rescue” / reset them on the floor when they encounter obstacles, errors, or require other support.
AMR
AMRs do not require under-floor wiring, magnetic tape stripes, or any other costly, time-consuming modifications to do their job. This means it is much faster, easier, and more cost-effective to get AMRs up and running—immediately adding new efficiencies. Even though AMRs may be slightly more expensive per robot, the low upfront costs and fast process optimization offer a rapid ROI (often in less than six months). AMR’s quick, cost-effective implementation makes expanding adoption across a warehouse or distribution center easy with minimal costs or disruption to overall productivity.
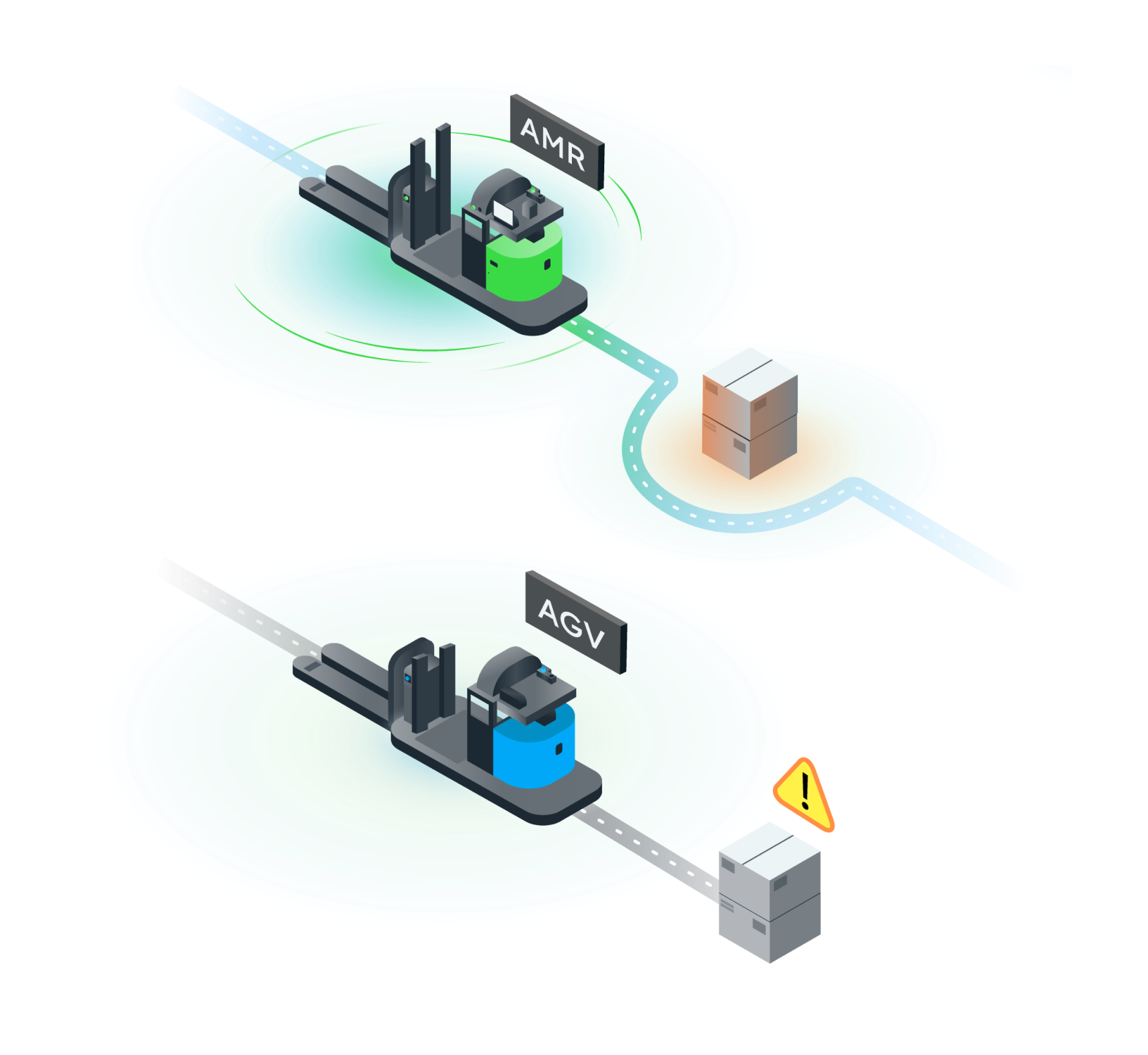
How AGVs Have Evolved into AMRs
AGVs remain an effective, proven technology for the right applications, but recent advancements in self-driving technology have pushed AMRs to the forefront of material handling automation. The main difference is AMRs’ intelligence and flexibility, significantly enhancing their ability to offer greater efficiency to a broader range of workflows and environments.
AGV: Fixed routes
AGVs follow a fixed, prescribed path. Whether this is defined by magnetic tape, embedded wires, laser targets, QR codes, or is even an infrastructure-free, lidar- / camera-based “virtual” path – if an obstacle blocks the route, the AGV will stop and wait for its path to be cleared, requiring human intervention and inhibiting productivity for both the worker and AGV.
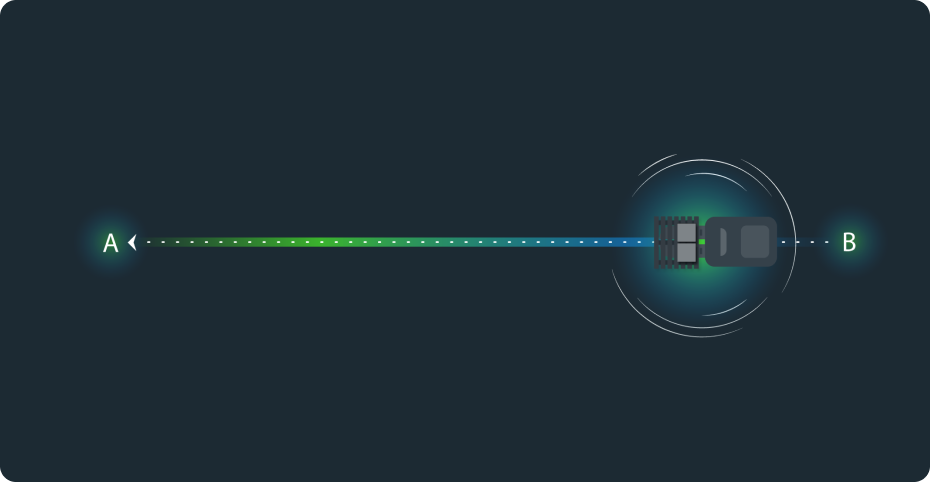
AMR: Flexible navigation
AMRs use advanced sensors and onboard AI to create a map of a facility in their memory with the ability to connect and plan routes between any destination in the facility. If an obstacle blocks the route, this contextual understanding allows the AMR to evaluate its current situation and safely reroute without assistance, resulting in higher system performance and uptime, and boosting productivity for both workers and AMRs alike.
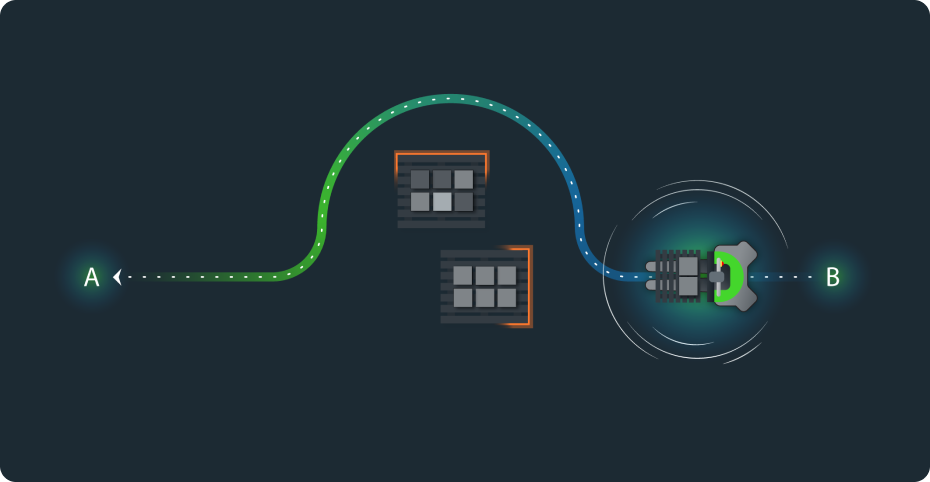
Dynamic recovery
Pallet Picking
Dynamically adjusts to fork pockets when picking pallets. Pallets do not need to be precisely placed
Requires payloads to be precisely aligned and positioned. Often needs human intervention
Path Adaptation
Detects obstacles and executes alternate routes around them
Executes basic collision avoidance
Navigation Recovery
Verifies its location and searches for an alternate route
Comes to a stop when localization is lost and requires a manual reset
Real autonomy
The gains created by path planning, obstacle avoidance, and pallet detection give AMRs the upper hand when it comes to efficiency and flexibility.
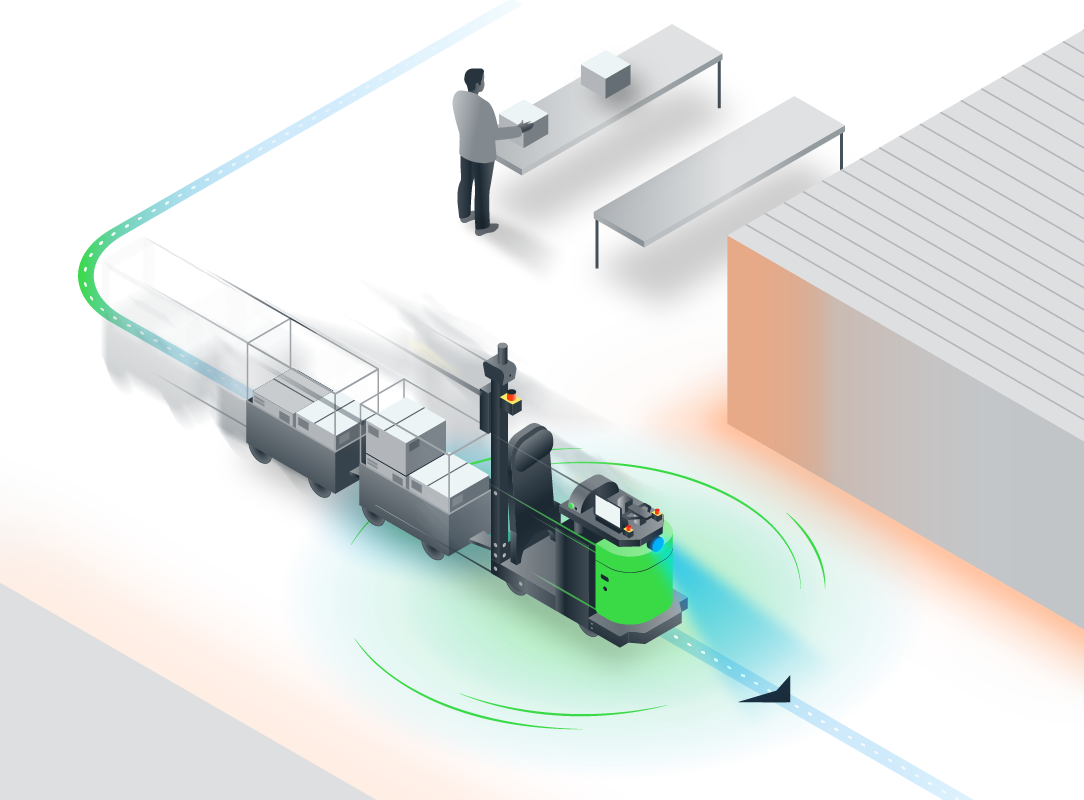
Continuous learning, always improving
Vecna Robotics’ AMRs adapt and learn from their environments. They share knowledge with the whole fleet, making expansion quick and easy.
Robots as a Service
Modern pricing, as a service
Get the material handling tech you need when you need it, all for a single, low annual fee. With Vecna Robots as a Service (RaaS) you can easily increase your material handling fleet as demand surges, or alter your system as your needs change.
Don’t let lengthy capital budgeting cycles slow you down. Rapidly deploy our system for your most critical workflows and turbo-charge your throughput in no time.
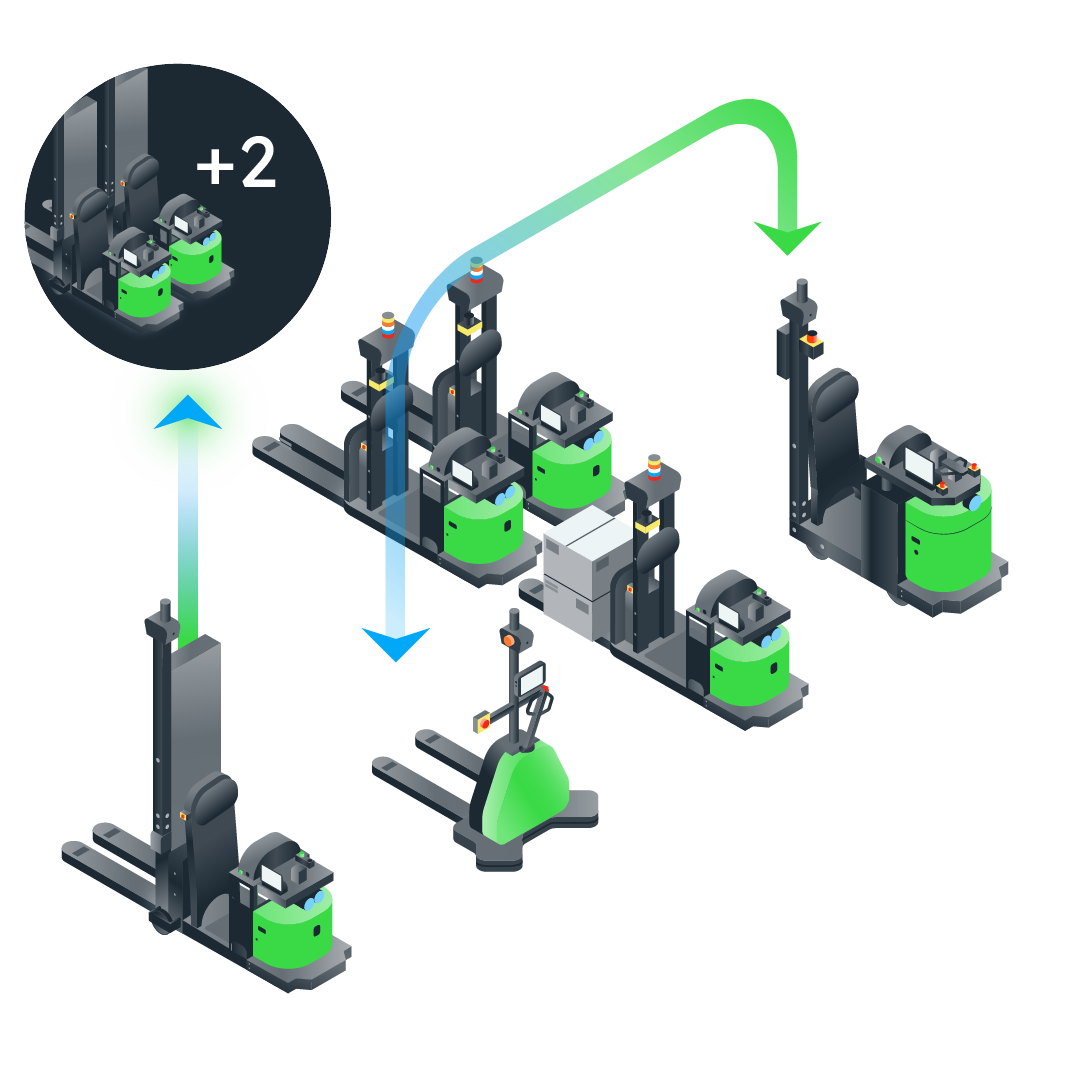
Frequently asked questions
What are the main advantages of using AMRs over AGVs?
AMRs offer superior flexibility, scalability, and performance compared to AGVs. AMRs actively locate and map their positions using advanced sensors, enabling real-time obstacle avoidance and adaptive navigation, while AGVs follow fixed routes, sometimes even requiring physical infrastructure in order to navigate.
How do AMRs contribute to cost reduction and a faster return on investment (ROI)?
Both AGVs and AMRs focus on reducing non-value-added travel, improving productivity and optimizing material handling operations. However, AMRs’ adaptability and flexibility support more dynamic workflows and environments, while their advanced navigation technology results in faster commissioning and less manual intervention / support than AGVs. These factors contribute to up to a 2x faster return on investment (ROI) when compared to traditional Automated Guided Vehicles (AGVs).
How does the flexibility of AMRs benefit warehouse operations?
AMRs’ ability to adapt—such as the ability to detect and adjust to varying payloads or adjust routes in real-time—enables them to operate in a broader range of use cases, environments, and operating scenarios vs. AGVs. This adaptability enhances operational efficiency, reduces downtimes, and accommodates changing workflows without the need for manual intervention.
What is the impact of path planning on AMRs’ efficiency and accuracy?
Even though AMRs can deviate from their nominal paths, this does not result in reduced navigational accuracy or efficiency. AMRs are just as capable as AGVs at precision docking maneuvers, and the ability to circumvent path blockages or choose an alternative route typically results in higher efficiency in busy warehouse environments vs. getting deadlocked and waiting for manual intervention to clear a fixed path.
Can AMRs be easily scaled up to meet evolving warehouse demands?
Yes, AMRs offer scalability that allows businesses to expand their robot fleet based on changing operational needs. Their flexible and adaptive nature ensures seamless integration and deployment across various warehouse workflows.
Are there any hidden costs associated with using AMRs?
Unlike AGVs, which may require physical infrastructure to operate and come with substantial recommissioning and support costs whenever route changes or manual interventions are needed, AMRs are capable of adapting to these scenarios on their own. The all-inclusive nature of RaaS also ensures transparent pricing and eliminates hidden expenses.
Can AMRs operate efficiently in narrow or crowded spaces?
Yes, AMRs are designed to navigate in narrow aisles and crowded spaces with ease. Their advanced sensor technologies and intelligent obstacle avoidance capabilities enable them to maneuver efficiently and safely in complex warehouse environments.
What are the benefits and drawbacks of fixed routes vs. intelligent navigation?
AGVs follow predetermined routes guided by wires, magnetic strips, or sensors, requiring extensive installation. Their minimal onboard intelligence limits adaptability, as they can only follow simple programming instructions. In contrast, AMRs employ intelligent navigation through cameras, sensors, and laser scanners, constructing maps and autonomously navigating without fixed routes. This flexibility allows AMRs to detect obstacles, maneuver around them, and optimize material flow, making them preferred in dynamic environments.
How do AMRs offer more flexibility in your operations that AGVs?
AGVs are constrained by fixed routes, limiting their applications to repetitive tasks. Their inability to easily adapt to changing functions or environments makes them less versatile. AMRs, on the other hand, offer high flexibility, performing various tasks with simple software adjustments. Their adaptability to changing environments and production requirements makes AMRs a preferred choice for businesses aiming to enhance productivity and responsiveness.
What robots work best in traditional vs. dynamic environments?
AGVs, rooted in traditional business models, struggle with adaptability in changing production environments. Their reliance on fixed routes and extensive infrastructure makes them less suited for agile and dynamic industries. Conversely, AMRs are designed for agility and flexibility, seamlessly adapting to changes in production lines or product variations. This makes AMRs ideal for modern manufacturing environments that require responsiveness to market demands.
What are the key investment considerations when comparing solutions?
AGVs demand a higher initial investment due to fixed-route infrastructure requirements, leading to disruptions during installation. Their inflexibility incurs additional costs when adapting to evolving business needs. In contrast, AMRs, with their intelligent navigation, offer a more cost-effective solution. Their minimal infrastructure modifications and rapid deployment result in faster process optimization, yielding a quicker return on investment.
What is the difference between autonomy vs. set routes?
AGVs operate on fixed routes, relying on markers such as wires, magnetic strips, or laser paths. In contrast, AMRs move autonomously, using maps uploaded or created dynamically. Equipped with cameras and sensors, AMRs calculate optimal routes in real-time, adapting to changing conditions and obstacles.