While AGVs and AMRs perform similar tasks, there is a large variance in their methods and in the capabilities that stem from them. Both, as a baseline function, are able to transport materials through industrial facilities and effectively reduce the need for manually operated machinery. However, the efficiency gains generated will depend on the distinct abilities of your robot’s competencies in navigating your facility and accomplishing its tasks in a dynamic environment. Understanding the varying abilities of AGVs and AMRs in path-planning and navigating will help guide those automating toward the best investment.
Traditional AGV Navigation: Path-Following
Traditionally, AGVs navigate using infrastructural landmarks, such as wires, magnets, tape, reflectors, or QR codes placed throughout the facility. Any AGV will rely on one or many of these features, moving along predetermined paths like a train on a track. Because these features are permanently and geographically set from the start, the robot is limited to operating on these fixed routes. This means any changes would require further infrastructural updates, newly planned routes, and a loss of valuable operating time.
AMR Natural Feature Localization
AMRs, and some advanced AGVs, employ a technique called natural, feature-based localization. Using a combination of Lidar and camera-based sensors to make a virtual map of its environment in real-time, the robot locates static features such as walls, racking, and pillars and uses these features to orient itself. Due to this, AMRs are not confined to any specific route and are able to navigate dynamic and ever-changing environments easily. Paths can be changed or interrupted with little consequence. This method forgoes the inconvenience and cost of infrastructure changes associated with traditional AGV installation and provides a more flexible form of navigation.
While advanced AGVs will claim that the integration of localization is the only necessary differentiating factor, there are more advanced technologies integrated into AMRs that allow them to vastly increase efficiency and decrease the need for human intervention, making them truly autonomous vehicles that provide the highest return. The winning factor that keeps AMRs mobile and working is path planning.
AMR Path Planning
What truly distinguishes the best AMRs from the rest of the pack is their uniquely intelligent ability to engage path-planning. In essence, path-planning is what it sounds like: robots with this feature will choose the most efficient route to accomplish their task, taking into account a multitude of actively changing environmental factors. In addition to using natural feature localization, path-planning AMRs are able to adapt to their environment and reassess routes as a human would. When AMRs encounter obstacles, they can reroute efficiently and get back on task – saving workers from having to unblock a gridlock caused by a stuck AGV.
Vecna Robotics has employed a combination of path-planning and natural feature localization that mirrors how a human thinks. Humans use input from their eyes to assess and navigate their environment. In much the same way, an AMR will actively use sensory data capture to navigate. The AMR can move around effectively using real-time intelligence rather than initial inputs of precise measurements of the warehouse. An AMR that relies on a combination of obstacle avoidance, smart localization and path planning will not be thrown by an environment in flux. The AMR’s performance will never degrade as the facility changes – in fact, it has the potential to improve its performance over time.
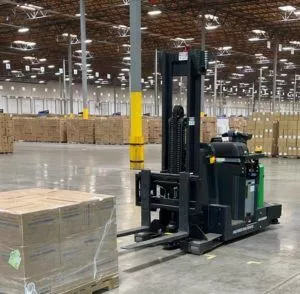
AGVs vs AMRs: Mobile Robots the Clear Winner in Navigation
AMRs apply natural feature localization in a way that makes for an easily integrated, flexible solution. Moreover, when paired with path planning technology, like in Vecna Robotics’ self-driving tuggers, fork trucks, and pallet trucks, the robots are more robust to changing environments and workflows, and require less support from workers. Thus, all resources can continue carrying out their work with as little interruption as possible.
Read about how path planning, obstacle avoidance and pallet detection set AMRs apart from AGVs.
Download our White Paper : Everything you need to know about AMR Navigation.