One of the more distinguishing features of AMRs is their fine-tuned ability to avoid obstacles. As discussed in this article about localization, AGV robots navigate using features installed within the facility. They follow distinct paths and are not able to reroute, in most cases requiring human intervention when unknown elements are introduced. AMRs use a more advanced technique of obstacle avoidance, providing increased efficiency and a richer return on investment.
AMR Obstacle Avoidance vs. AGV Collision Avoidance
Both AMRs and AGVs are enabled with collision avoidance. At a minimum, their safety system will sense any blockage and safely slow or stop the robot before a collision occurs. However, this is typically the limit of what AGVs can accomplish. AMRs, on the other hand, have obstacle avoidance. The robot is not only able to avoid collisions, but can reroute and continue its task as a human would.
In a dynamic warehouse environment, obstacle avoidance is crucial. With only basic collision avoidance, AGVs need to be monitored more frequently. Any obstacle – say, packaging that has been discarded, or another vehicle – will need to be moved by a human. These frequent interruptions consume workers’ time, often depleting labor resources that are better used elsewhere. This level of interaction undermines much of the purpose of integrating warehouse robots in the first place.
AMRs possess capabilities much closer to true autonomy. They are able to fix problems themselves, and add value on a more consistent basis by not interrupting other workflows.
AMR and AGV Robots in Traffic Congestion
Just as all mobile robots have the ability to detect an obstacle and avoid collision, all mobile robots also have what are known as safety fields, or speed-limited zones. In these areas, robots are programmed to slow or stop, and take a certain amount of buffering time before continuing their task. AGV vendors program these locations into the robots during the mapping process.
However, its important to mention again that warehouses are dynamic environments. An area that was not being used when the AGV was installed could become the busiest hub in the facility, and that which was originally a high traffic area goes unused. This could be handled in one of two ways:
- Firstly, the AGV may detect traffic and slow in the newly busy area, and also continue to slow down as programmed in the original, but now empty area unnecessarily. This is a drag on the efficiency of the vehicles.
- Secondly, the AGV may be programmed to ignore traffic in the previously-empty, now high-traffic area and speed through it. This is a major safety concern.
The path planning abilities of AMRs offer a fix to this problem, adjusting not only speed, but direction. Robots using this technology use intelligent analytics to chose the most efficient route to complete their task, taking traffic and obstacles into consideration in real time. While AGVs are limited to waiting until their path is clear, AMRs can venture briefly off path to route around traffic at a safe distance, providing plenty of room for other actors to complete tasks. If this is not the most efficient choice, AMRs will choose a new route entirely.
Dynamic Obstacle Avoidance: Passing Moving Vehicles
AGVs – or even some AMRs – employ limited obstacle avoidance, diverting for their path for only a short distance to avoid static obstacles. While this works in isolated incidents, it is not enough in congested areas. Moving vehicles are a frequent feature of industrial spaces, and AMRs are much better equipped to succeed in these interactions.
AMRs know the rules of the road. They are designed to share space with manually operated vehicles, other AMRs, and AGVs, and move seamlessly with other objects and entities in its shared space. In a situation where an AMR meets oncoming traffic, it can move to the side to pass, wait until the coast is clear and then resume its mission. In this same instance, an AGV would stop because it would perceive the moving object as an insurmountable challenge. It could then block traffic altogether and require an operator to intervene.
The Benefits of AMRs over AGV Robots
In most dynamic warehouse environments, goods are moving quickly and workflow or floor plans change frequently. A path following AGV is not able to handle these changes. A site manager must manually re-route the AGV robot to teach it a new route. These interventions are interruptive consume workers’ time. AMRs avoid obstacles in a way that is superior in providing unmatched autonomy. They are much more equipped to function without assistance, giving floor managers peace of mind, and optimized, autonomous workflows.
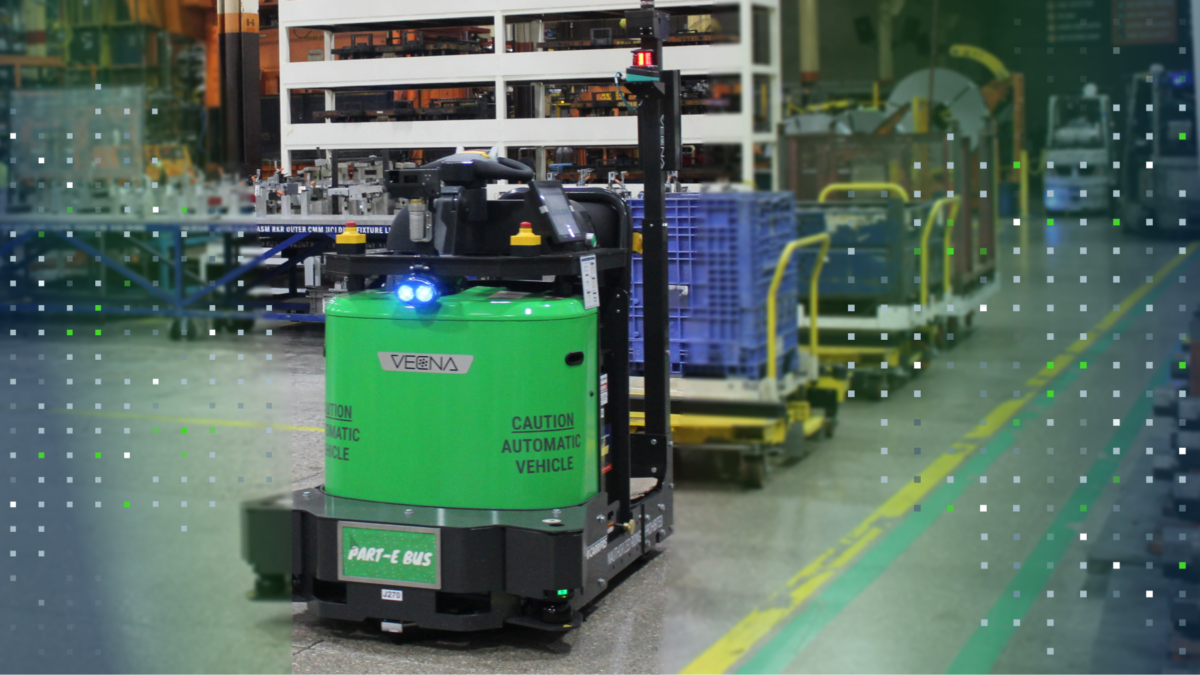
Autonomous Mobile Robots, like self-driving tuggers, fork trucks, and pallet trucks, apply obstacle avoidance technology in a way that maximizes safety and efficiency.
For more about the differences between the AMR and the AGV, download the white paper.