What is an AGV?
AGV Robots, also known as Automated Guided Vehicles (or just AGVs), have come a long way since their early beginnings. Originating in the 1950s, these robotic vehicles were initially designed to perform singular, repetitive tasks, guided along their paths by magnetic tapes or wires embedded in the factory floor. This rudimentary form of navigation allowed for the straightforward transportation of materials and goods within manufacturing plants and warehouses, laying the groundwork for the automated logistics systems we see today.
Over the decades, AGVs have undergone remarkable advancements, evolving from their simplistic predecessors into sophisticated, multi-functional machines capable of navigating complex environments with precision and efficiency. Today’s AGVs are equipped with a variety of navigation systems, including laser guidance, GPS, and computer vision, enabling them to understand and interact with their surroundings in real-time. This leap in technological capabilities allows AGVs to perform a wider range of tasks beyond mere transportation, including loading and unloading goods, picking and placing items, and even conducting inventory checks.
The evolution of AGVs has been driven by the increasing demands of modern businesses facing rising labor costs and challenges associated with worker scarcity. In this context, AGVs offer a compelling solution, providing a means to automate repetitive and labor-intensive tasks, thereby reducing reliance on human labor and minimizing operational costs. Furthermore, the adaptability and scalability of AGV systems make them an ideal choice for businesses looking to enhance their operational efficiency and responsiveness to market demands.
As AGVs continue to integrate advanced technologies such as artificial intelligence and the Internet of Things (IoT), their role within industrial and logistical operations is set to become even more central. These intelligent vehicles can now collaborate with other automated systems and human workers in a cohesive, flexible workflow, paving the way for the factories and warehouses of the future. Through their continuous evolution, AGV Robots exemplify the transformative power of automation, offering a glimpse into a more efficient, productive, and adaptable industrial landscape.
In this article, we’ll first explore how AGVs work, then dive into five of the ways that AGV robots have matured. With these advancements in technology, it’s clear why AGV robots are gaining traction in automating logistical operations within warehouses, manufacturing plants, and distribution centers. Their enhanced capabilities and versatility underscore their growing appeal in streamlining tasks that are crucial to the operational efficiency of these facilities.
How do AGVs work?
Understanding the operational mechanics behind AGV Robots, or Automated Guided Vehicles, reveals a fascinating blend of technology and precision that powers these invaluable assets within industrial settings. While the previous sections have journeyed through the evolution of AGVs from their inception to the present day, a closer look at their functionality provides deeper insights into their integral role in modern logistics and manufacturing processes.
At their core, AGVs are designed to autonomously navigate through facilities, carrying out a variety of tasks ranging from material transport to inventory management. The initial AGVs were relatively straightforward in their operation, relying on physical cues like magnetic tapes or embedded wires to guide their paths. This method, while effective for consistent and unchanging routes, presented limitations in adaptability and flexibility, essential traits for dynamic industrial environments.
Modern AGVs, however, have significantly transcended these early navigation methods, incorporating advanced technologies such as laser guidance, GPS, and computer vision. These technologies enable AGVs to comprehend their surroundings in a more nuanced manner, allowing for real-time decision-making and route adjustment. This leap in navigational capabilities is pivotal for adapting to the constantly changing landscapes of warehouses and production floors.
The integration of sophisticated sensors and artificial intelligence has also greatly enhanced the safety and efficiency of AGVs. Sensors detect obstacles and environmental changes, prompting AGVs to modify their paths accordingly, thus minimizing potential disruptions and ensuring seamless operation. AI algorithms optimize routes and tasks based on various parameters, including distance, priority, and operational demand, ensuring optimal performance.
The adoption of cloud technology and IoT connectivity further amplifies the capabilities of AGVs. Through cloud connectivity, AGVs can receive updates, share operational data, and coordinate with other automated systems in real-time, fostering a collaborative and highly efficient automated ecosystem. This connectivity ensures that AGVs are always operating with the latest software, equipped with the most current navigation maps, and synchronized with the overall operational goals of the facility.
Through sophisticated navigation systems, advanced sensors, AI, and cloud connectivity, AGVs have become indispensable tools for industries looking to enhance efficiency, safety, and adaptability in their operations. As these technologies continue to evolve, so too will the capabilities and applications of AGVs, further solidifying their role in the future of industrial automation.
How have AGV robots evolved?
Navigation: obstacle avoidance and autonomous rerouting
How AGV robots navigate is the most fundamental aspect of their change. Traditional AGVs traveled exclusively along predefined routes, typically following magnetic tape or other types of lines demarcated on the floor. This is still true of many AGV robots today. Using this earlier method, the plant operator must create the pathways by applying magnetic tape to the surface of – or embedding wires into – the floor, or attaching beacons to walls or fixed equipment. With such technology, when the AGV robot encounters an obstacle, it will slow down or stop and call for help. A human must come to the rescue and clear the AGVs path before it can continue. In a dynamic environment like a warehouse or factory, in which vehicles are moving around all the time, and pieces of packaging are frequently discarded, the inability to avoid obstructions is a significant drawback.
On the other hand, modern AGV robots, often called Autonomous Mobile Robots (AMRs), store a map of the facility in their navigation system. With this sophisticated technology, AMRs can swerve around obstacles in their path if it is safe to do so. If a minor path correction isn’t enough, the AMR robot can plot out an entirely new route to its destination. Vecna’s differentiated approach to navigation is focused on advanced localization and path planning, which we believe are the most efficient and safe way to move raw materials faster and optimize automated throughput.
In studies done by Vecna Robotics, 80% of trips taken by their AMRs involved using obstacle avoidance. Without the ability to circumvent obstructions, an employee would have had to clear all those blockages, taking them away from more important responsibilities and limiting the usefulness of the AGV.
For more on the distinctions between AGVs and AMRs, see the white paper:
Everything you need to know about AMR and AGV Navigation and why it matters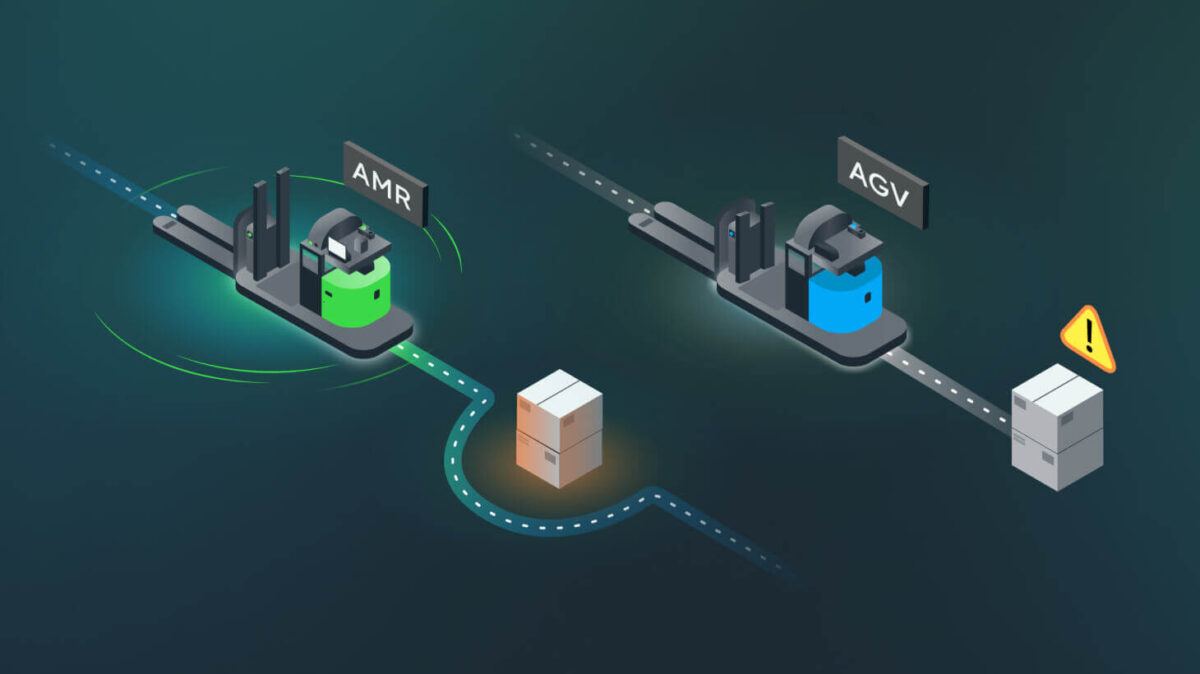
A suite of sensors: better safety and navigation system
Yesterday’s AGV robots had a limited number and type of sensors, typically proximity sensors that told the machine there was something – the AGV wouldn’t know what – was in the way.
Today’s AGV robots have a complex navigation systems that include wide range of sensors that operate together. Modern AMRs combine multiple vision and LiDAR (laser) sensors for full 3D sensor fusion perception. This eye-like perception allows the Vecna AGV robots to navigate in high-traffic and unpredictable environments with confidence. Along with these sensors Vecna added a three-tiered safety architecture that exceeds ANSI B56.5, RIA 15.08, safety standards, and allows for both adaptive safety fields and intelligent, safe path planning.
Interoperability between AGVs and other robots
MassRobotics, an independent non-profit, recently released the MassRobotics Interoperability Standard to allow robots from different vendors to seamlessly interact. Vecna Robotics was one of the first participants in these standards, and offers an autonomous tugger, forklift and pallet truck that are AMR Interop certified and are now being tested cooperatively with other robots at a Fedex Ground location. Such interoperability means that a warehouse that has been using a pick and place robotic system from one vendor can use a pallet truck from another vendor. Not only can the robots pass off goods from one to the other, they can also exchange information. The data can be displayed on a share dashboard and allows the facility operator to see a real time overview of the functioning of their robot fleet.
Collaboration with human workers
The relationship between AGVs (Automated Guided Vehicles) and human workers has evolved significantly, reflecting a shift towards collaborative and interactive work environments. Modern AGVs are designed with sophisticated safety protocols and advanced detection systems, enabling them to share operational spaces with humans safely. This technological advancement allows for seamless cooperation, with AGVs adjusting their paths in real time to accommodate human movements, thereby ensuring both productivity and safety in shared environments.
Further enhancing this collaboration, the integration of smart wearables has revolutionized how employees interact with AGVs. Workers equipped with IoT-connected devices can directly communicate with these automated vehicles, optimizing workflows and adapting operational strategies on the fly. This level of interconnectivity not only streamlines processes but also fosters a dynamic and responsive work setting, where humans and machines work in harmony to achieve common goals.
This harmonious integration of AGVs into the workforce underscores a broader commitment to creating inclusive, safe, and efficient work environments. By prioritizing cooperation and safety, businesses are leveraging the full potential of their automated systems while ensuring their human employees feel valued. As we move forward, the fusion of human ingenuity with robotic precision will continue to shape the future of industrial operations, making the collaborative model between humans and machines a cornerstone of industrial success.
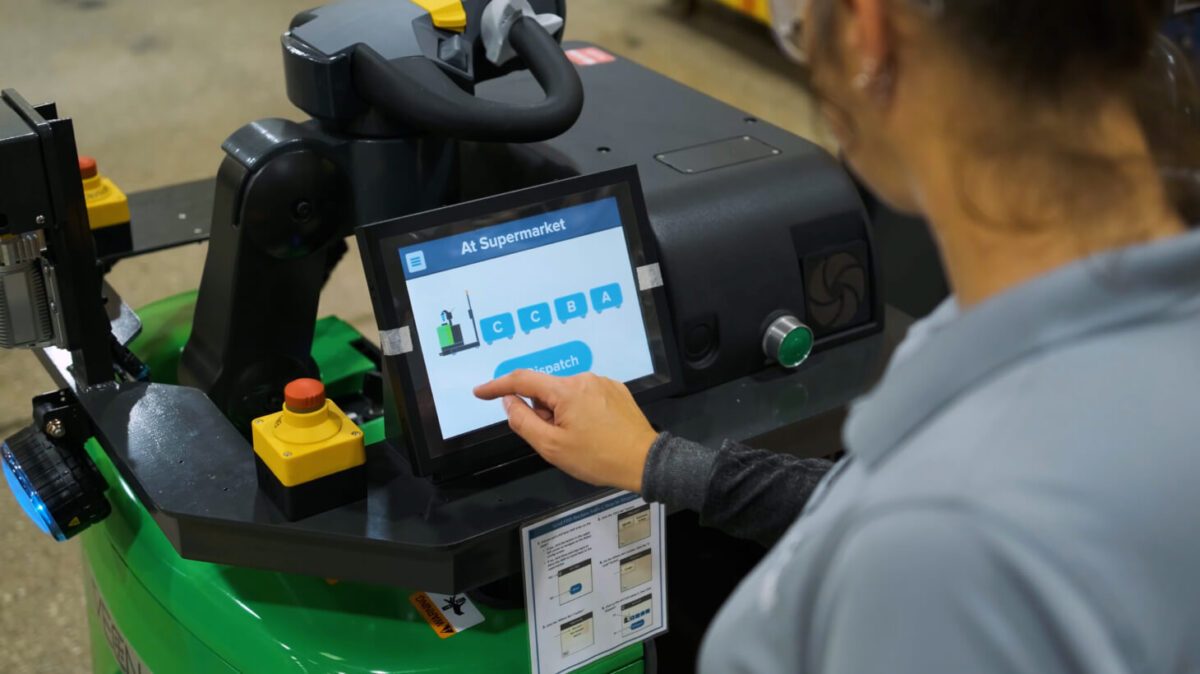
Cloud-enabled artificial intelligence means more possibilities
The integration of cloud-enabled artificial intelligence (AI) into AGV robots marks a significant leap forward in the field of industrial automation, opening up a realm of new possibilities. This technological synergy not only enhances the autonomous capabilities of AGVs but also enables a level of intelligence and adaptability that was previously unattainable. Through the cloud, AGVs are constantly learning from each other, sharing experiences and solutions across an entire network. This collective intelligence means that an improvement or a lesson learned by one robot can instantly benefit the entire fleet, leading to a rapid and continuous cycle of improvement that drives efficiency and productivity to new heights.
This cloud-based AI integration also allows for predictive analytics and maintenance, ensuring that AGVs can self-diagnose potential issues and perform preventive maintenance. This capability drastically reduces the risk of unexpected downtimes, ensuring a smooth and uninterrupted flow of operations. Furthermore, it enables AGVs to adapt to changing operational demands in real-time, optimizing their routes and tasks based on the current workload and operational priorities. This level of dynamic adaptation ensures that AGVs are always operating at peak efficiency, contributing to a more resilient and flexible operational framework.
In essence, cloud-enabled AI transforms AGVs from mere tools for automation into intelligent partners in the operational process. This evolution not only amplifies their utility but also integrates them more deeply into the strategic fabric of logistics and manufacturing operations. As AGVs continue to evolve with AI and cloud technology, they stand at the forefront of industrial innovation, reshaping the landscape of automation and setting new standards for efficiency, adaptability, and intelligence in the modern workplace.
Applications of AGVs
Automated Guided Vehicles (AGVs) have found their place at the heart of industrial innovation, serving a myriad of applications across various sectors. These versatile robots have transcended their initial role of simple task performers to become critical components in the intricate dance of modern logistics, manufacturing, and beyond. Their deployment in warehouses and factories around the globe has not only streamlined operations but also propelled these environments toward unprecedented levels of efficiency and productivity.
In the realm of warehousing, AGVs are instrumental in automating the internal movement of goods, from receiving to shipping. They ensure that products are moved swiftly and safely across the warehouse floor, reducing manual handling and the associated risks. This automation extends to inventory management, where AGVs equipped with scanning capabilities can perform regular stock checks, updating inventory levels in real-time and ensuring accuracy in order fulfillment. Moreover, in distribution centers, AGVs play a pivotal role in sorting and staging products for delivery, optimizing the dispatch process and minimizing errors.
Manufacturing facilities leverage AGVs to facilitate a seamless flow of materials through production lines. From supplying raw materials to machines at the start of the production process to transporting finished goods to the storage area, AGVs ensure a constant and consistent supply chain. Furthermore, their application in assembly lines, where precision and timing are paramount, showcases their ability to adapt to complex manufacturing processes and contribute to the reduction of production times and costs.
The applications of AGVs are continually expanding, driven by advancements in technology and the growing need for automation in response to global trends such as e-commerce growth, customization demands, and the push for sustainable operations. As businesses seek to navigate the challenges of the modern industrial landscape, AGVs stand ready to offer solutions that are not only efficient and reliable but also scalable and adaptable to the ever-evolving market needs.
Most common types of AGV robots in use today
As AGV technology has matured, a variety of models have emerged to cater to different industrial needs, each with unique capabilities and applications. Among the most common types in use today are tow vehicles, unit load carriers, pallet trucks, and autonomous mobile robots (AMRs), each serving distinct roles within logistics and manufacturing environments. Tow vehicles, for example, are adept at moving large quantities of materials across facilities, ideal for tasks that require the transportation of heavy loads over long distances. Unit load carriers offer precision and efficiency in moving individual items or small loads, optimizing the handling of goods with their ability to navigate to specific locations for pickup or delivery.
Pallet trucks have revolutionized the way pallets are moved within warehouses, offering a flexible solution for transporting and positioning pallets without the need for manual forklifts. This not only speeds up the process but also enhances safety by reducing the need for human interaction with heavy loads. Meanwhile, AMRs represent the pinnacle of AGV development, boasting advanced navigation systems that allow for free movement within dynamic environments. These robots can adapt their routes in real-time, making them perfect for environments where flexibility and adaptability are key.
The primary benefits of AGVs
The adoption of AGVs across various industries brings a multitude of benefits, key among them being enhanced efficiency, improved safety, and significant cost savings. By automating repetitive and labor-intensive tasks, AGVs free up human workers to focus on more complex and value-added activities, thereby increasing overall productivity. This efficiency gain is complemented by the precision and reliability of AGVs, which minimize errors in tasks such as material transport and inventory management, ensuring accurate and timely operations.
Safety is another critical area where AGVs make a significant impact. By taking over tasks that are hazardous for humans, such as transporting heavy loads or operating in environments with potential chemical or physical hazards, AGVs reduce the risk of workplace accidents and associated liabilities. Furthermore, the implementation of AGVs leads to cost savings in the long run. Although the initial investment may be significant, the reduction in labor costs, combined with increased productivity and reduced error rates, results in a compelling return on investment.
The future of AGVs looks promising as continuous advancements in technology further expand their capabilities and applications. As industries strive to meet the growing demands of the modern market, AGVs will undoubtedly play a pivotal role in shaping efficient, safe, and adaptable operations.
Need to know more?
Want to learn more about what modern robotic material handling equipment can do for you? Contact us and speak with a knowledgeable and experienced automation expert who can help you on your automation journey.