Pivotal™ Autonomous navigation
Feel the need for speed
Pivotal™ Autonomy drives the fastest, smartest, highest performing and most robust autonomous material handling equipment on the market.
Superior Sensor Technology
Navigate challenges with AMRs equipped with real vision
Vecna’s AMRs combine multiple vision and lidar sensors for full 3D sensor fusion perception.. This eye-like perception allows our robots to navigate in high-traffic and unpredictable environments with total confidence.
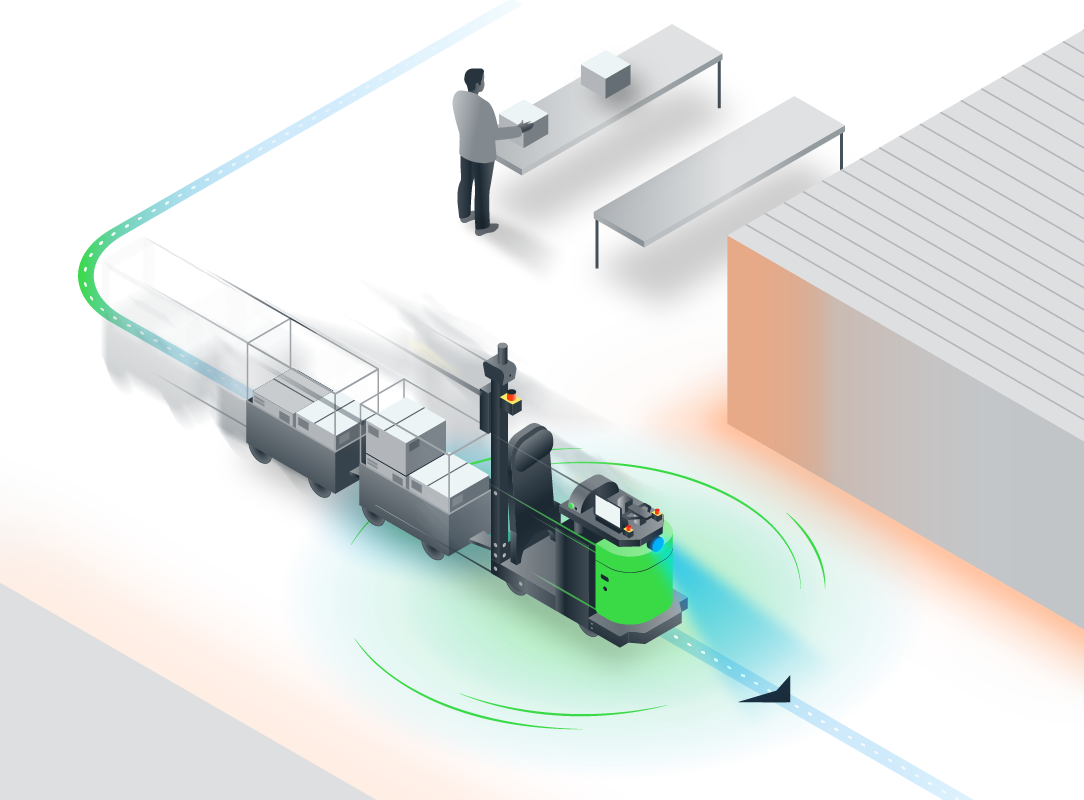
INDUSTRY LEADING AUTONOMY
Speed, safety and performance
Power-up your operation with the fastest, smartest, highest performing and most robust autonomous material handling solution on the market.
33%
throughput improvement vs. manual operations
1.5x
more pallets moved per $ vs. manual MHE
99.9%
uptime with Pivotal™ autonomy and remote monitoring
0
safety incidents with 3-tier safety architecture
How our navigation works
Move thousands of pallets the easy way
Vecna Robotics’ navigation starts with a virtual map of your entire facility and then the autonomy kicks in.
Step 1: Map
Vecna creates a virtual map of your entire facility’s operating area.
Step 2: Program
Your map is programed with pickup/drop-off locations and rules of the road.
Step 3: Synchronize
Our system connects all routes and synchronizes with all vehicles in your fleet.
Step 4: Route
Each Vecna AMR plots the best available route to complete their missions.
Step 5: Adapt
Vecna’s AMRs safely deviate from prescribed route to avoid obstacles.
Step 6: Go
If congestion is too high on the prescribed route, Vecna’s AMRs will pursue alternative available paths to keep moving.
Your Robot Journey
From no bot to robot at the speed of your business
Your system can be deployed in as little as a few weeks and get to scale as your needs expand.
1 Discover
Identify and prioritize your pain points, choose workflows to focus on, get initial quote.
2 Design
Design solution, approve requirements, obtain sign-offs, and establish start date.
3 Deploy
Rapidly install, run a limited-scale demo that meets KPIs and familiarizes users, on-site training.
4 Learn
Ramp up to full production, 24/7 monitoring by our Command Center, customer success provides bi-weekly analytics and training.
5 Scale
Expand automation to new workflows at the existing site and identify new sites for program growth.
Trusted by industry leaders
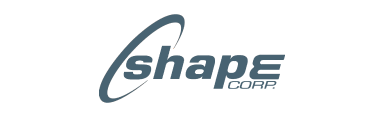
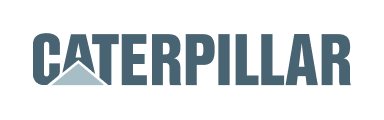
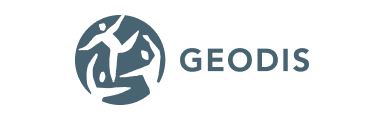
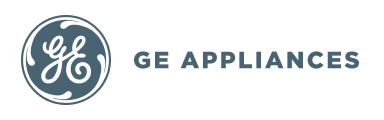
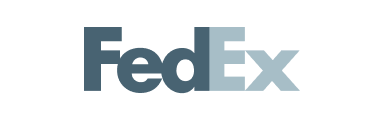
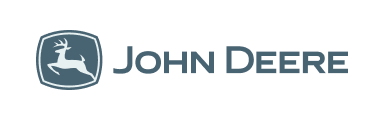
and those in the know
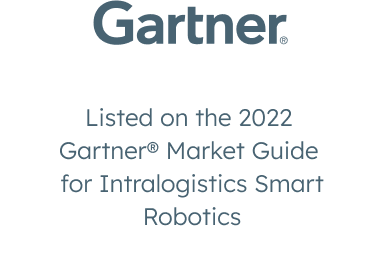
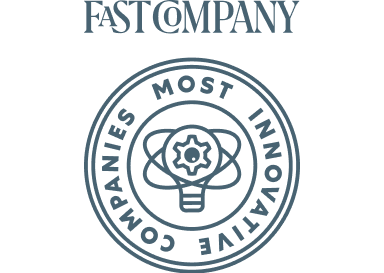
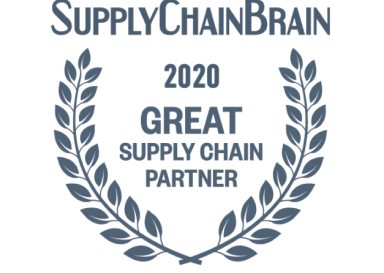
Let’s go
Optimize your critical workflows right now
Have questions about what Vecna can do for you? Tell us about yourself and an automation expert will be in touch shortly.
Thank you for getting in touch
We aim to respond to all messages within 1-2 business days.
In the meantime you might be interested in some of these resources.