Within the last decade, Automated Guided Vehicles (AGVs) have undergone a significant transformation. The automated guided vehicle of yesteryear was relatively inflexible and inefficient compared to today’s Autonomous Mobile Robots (AMRs).
Warehouse operations have traditionally relied on manual labor for material transport, but the emergence of Automated Guided Vehicles (AGVs) in the early 1960s marked a turning point. Initially, AGVs followed pre-defined paths using wires embedded in the floor. Their technology evolved in the 1970s and 1980s to include navigation methods like magnetic tape and laser guidance, thereby broadening applications beyond mere transport. By integrating with Warehouse Management Systems (WMS) in the late 20th century, AGVs began to coordinate operations across warehouses, distribution centers, and hospitals.
The ongoing technological advancements have led to a new generation of AGVs in the 21st century, becoming a complex and vital part of material handling automation. Today, they often work alongside or are replaced by more advanced Autonomous Mobile Robots (AMRs). These next-gen AMRs are revolutionizing material handling by leveraging the latest self-driving technology, offering greater efficiency and accuracy, reducing labor costs, and minimizing workplace risks associated with human-operated equipment.
The differences between early AGVs and today’s AMRs are striking.
Fixed routes versus flexible pathways
The Automated Guided Vehicles of the recent past—and many still today—follow a fixed, prescribed pathway, similar to trains. Various techniques are used to define the paths for AGVs, including tape on—or wires embedded into—the floor. Other methods of prescribing the pathway are possible, such as QR codes or other visual markers attached to the walls, columns, or fixed equipment, including recent advancements utilizing infrastructure-free methods such as lidar.
However, like a train, the AGV cannot deviate from its predetermined path. If an obstacle blocks the route of an AGV, it is programmed to stop and wait for its path to be cleared. And if any adjustments are needed, the entire route must be recommissioned.
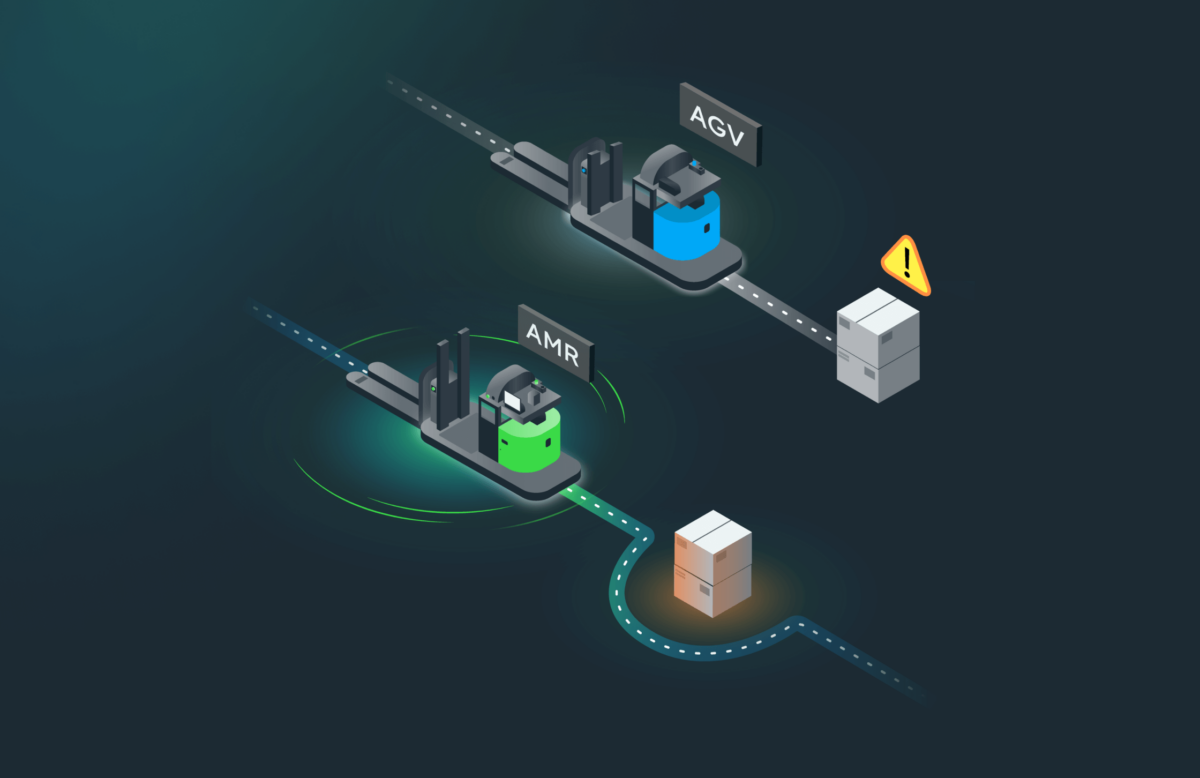
In contrast, modern Autonomous Mobile Robots employ a technique called natural, feature-based localization. Using a combination of Lidar and camera-based sensors to make a virtual map of its environment in real time, the robot locates static features such as walls, racking, and pillars and uses these features to orient itself. Due to this, AMRs are not confined to any specific route and are able to navigate dynamic and ever-changing environments easily. Paths can be changed or interrupted with little consequence. This method forgoes the inconvenience and cost of infrastructure changes associated with traditional AGV installation and provides a more flexible form of navigation.
While advanced AGVs will claim that the integration of localization is the only necessary differentiating factor, there are more advanced technologies integrated into AMRs that allow them to vastly increase efficiency and decrease the need for human intervention, making them truly autonomous vehicles that provide the highest return. The winning factor that keeps AMRs mobile and working is path planning.
AMRs make sense of their environment
Advanced algorithms give robots the ability not just to sense their environment, but also to make sense of it. For example, modern automated material handling vehicles can distinguish between a human and a shelf or even different pallet types. Such contextual understanding of its environment is crucial for an automated vehicle’s safe collaboration with people.
Modern autonomous mobile robots use a variety of sensors and then combine the information into an integrated three-dimensional model. This capability, called sensor fusion, allows today’s material handling equipment to employ laser-based computer vision systems, optical cameras, and proximity sensors to increase operational safety and functionality.
Essentially if something blocks an AMR’s pathway, they can stop and wait for the blockage to clear, but can also simply swerve around the problem. Using advanced sensors and onboard artificial intelligence, the AMR can intelligently determine if there is enough space available and that it would be safe to perform this maneuver, or can autonomously plan and travel via an alternate path to its assigned destination.
Today’s robots are more effective than yesterday’s AGVs
How important is the intelligent obstacle avoidance capability of the AMR? Statistics gathered by Vecna Robotics show their AMRs use obstacle avoidance at least once during 80% of their assigned trips. That means if the automated vehicle could not circumvent roadblocks, either the vehicle would have to wait until the blockage cleared, or someone would have to travel to the site of the problem and remove the impediment. In either case, an automated vehicle’s efficiency suffers if it cannot handle obstructions.
Mobile robots excel in flexibility and ease of reconfiguration
When business conditions change, sometimes it becomes necessary to change the route an AGV will take. Because traditional automated guided vehicles travel an assigned path, a change in their course requires modifying the guidance markers or whatever infrastructure was used to define the pathways. These alterations take time and can be disruptive.
Modern autonomous mobile robots do not need such infrastructure because AMRs carry a facility map in their onboard computer storage. If the facility map changes, a new map can be easily and quickly installed.
Once one robot “learns” the map of a facility and its assigned pick-up and drop-off locations, this knowledge can be transferred to other AMRs. Therefore, augmenting operations with additional robots is simple and fast and does not require physical infrastructure modification.
Extending safety benefits into more areas
Safety remains a top concern in warehousing and transportation. For example, according to the Bureau of Labor Statistics, more than 34,000 people are seriously injured annually in the U.S. due to accidents involving forklifts.
AMRs represent a significant advancement in safety features compared to AGVs. Equipped with advanced sensors such as LiDAR, cameras, and radar, AMRs are capable of detecting obstacles and dynamically altering their routes to avoid collisions. Unlike AGVs, which often follow predetermined paths, AMRs can adapt on the fly to obstructions or sudden changes in the environment. This flexibility ensures uninterrupted operation and minimizes risks. Furthermore, modern AMRs are designed to recognize human presence and respond appropriately, ensuring safer coexistence in shared workspaces.
AMRs also offer real-time monitoring, integration into centralized systems, and compliance with the latest industry safety standards. Continuous monitoring provides real-time information on their status and location, and if a safety issue is detected, alerts can be sent to supervisors for immediate intervention. Compliance with contemporary safety standards further ensures that AMRs meet or exceed regulatory requirements, an aspect that might be lacking in older AGVs. Emergency stop functions are standard in both AMRs and AGVs, but AMRs often offer more intelligent engagement methods, adding an additional layer of protection.
The adaptability of AMRs through software updates is another key factor contributing to their safety advantage. Unlike many AGVs, AMRs can receive regular updates to enhance their safety features or align with new regulations. This continuous adaptability ensures that they remain at the forefront of safety standards over time. Collectively, these features, ranging from advanced obstacle detection to real-time monitoring and adaptability, make AMRs a safer and more efficient option in industrial environments, particularly where interaction with human workers is common or where rapid responsiveness to changes is essential.
While the AGVs of a decade ago were already safer than manual forklifts, AMRs bring safety to a new level. AMRs can sense their environment far better than AGVs and because AMRs can handle a broader range of workflows, their safety benefits can be extended into more use cases than AGVs.
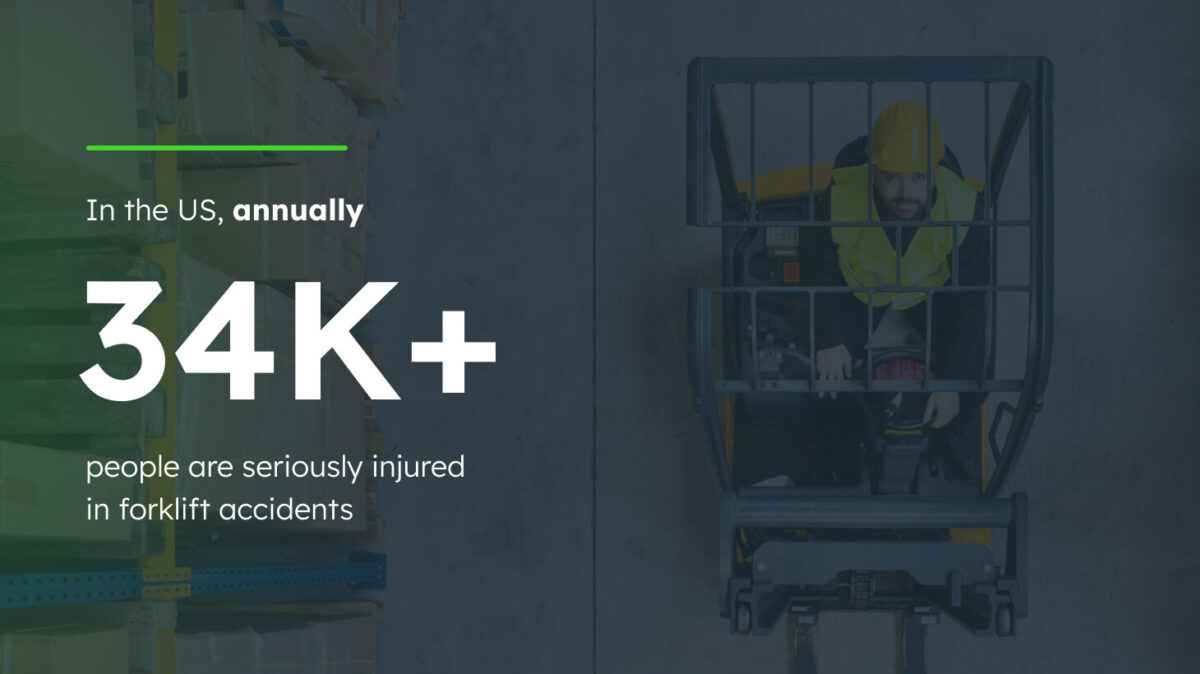
Robot collaboration and interoperability
Modern AMRs can be used in ways previous generations of AGVs could not. Today’s AMRs have acquired the ability to cooperate with other types of automation equipment. For example, an AMR forklift from Vecna Robotics can lift pallets to and from conveyors and wrappers. Such flexibility enhances the return on investment from AMRs by expanding the range of tasks they can accomplish.
To go into greater detail, AMRs integrate effortlessly with existing Warehouse Management Systems (WMS) and Enterprise Resource Planning (ERP) systems, allowing for real-time coordination with conveyors, sorting systems, and automated storage and retrieval systems (AS/RS).
AMRs also work in conjunction with collaborative robots (cobots), creating a more fluid and responsive production line, and they interact with automated picking systems to optimize efficiency in the retrieval and transportation of goods. Their integration with Internet of Things (IoT) devices and sensors enables them to respond to environmental factors and communicate with security and climate control systems.
Additionally, AMRs are scalable and adaptable to various automation technologies, offering customizable interfaces that can be tailored to specific industry needs. This multifaceted cooperation with different automation systems not only enhances overall efficiency but also ensures responsiveness and adaptability within an interconnected environment, positioning AMRs as key players in the evolving landscape of industrial automation.
AMR: A robot for all seasons
When comparing Automated Guided Vehicles (AGVs) and Autonomous Mobile Robots (AMRs), the fundamental difference lies in their adaptability and response to environmental changes. AGVs operate based on an initial mapping of the environment and expect it to remain constant. Since most industrial and warehouse settings are in a state of constant flux due to various operational needs, this static approach means AGV performance can degrade over time.
In contrast, AMRs are designed with flexibility and perception in mind, utilizing cloud-driven technology to adapt dynamically to their surroundings. Unlike AGVs, AMRs can plan an optimal path for each mission, even as the environment changes. They use sophisticated sensors and intelligent algorithms to understand and navigate the space in real-time, allowing for adjustments to obstacles or new configurations in the layout.
Additionally, AMRs are built to improve continuously throughout their useful life. As they gather more data and insights from each mission, they can enhance their performance, optimizing routes, reducing delays, and even predicting potential issues before they arise. This ability to learn and adapt provides not only a more efficient material handling solution but also a more resilient one. It allows AMRs to keep pace with the ever-changing demands of modern warehousing and manufacturing environments, ensuring they remain a valuable asset for a longer time.
In summary, while AGVs have been a substantial step forward in automation, AMRs represent the next evolution, offering greater flexibility, adaptability, and ongoing improvement. These characteristics make them a more suitable choice for the dynamic and complex needs of today’s industrial landscapes.
Consult our AGV vs. AMR guide for more information on the evolution of Automation Guided Vehicles and how they differ from modern AMRs. Or, contact Vecna Robotics today to speak with an experienced automation expert who can help you on your automation journey.