What is automation in warehousing?
Automation in warehousing encompasses the strategic integration of technologies such as robotics, artificial intelligence (AI), and the Internet of Things (IoT) to revolutionize how warehouses function. This technological infusion not only streamlines processes but also significantly enhances the precision and volume of output, addressing the growing complexities of modern supply chains. Industries ranging from grocery to automotive, and especially e-commerce, have been at the forefront of implementing these advancements, setting a benchmark for operational success.
The enthusiasm for automation within the supply chain community is overwhelmingly positive, as evidenced by a 2024 Gartner survey which revealed an astonishing 74% of supply chain professionals have adopted cyber-physical systems in their warehousing and manufacturing operations already with another 19% conducting active pilots. This surge in interest highlights a collective acknowledgment of automation’s critical role in bolstering competitiveness, sustainability, and resilience. As businesses navigate the challenges of globalization, customer demand, and the ongoing digital revolution, the strategic adoption of warehouse automation technologies is becoming an indispensable element of their operational strategy, promising not only to enhance current performances but also to shape the future landscape of global supply chain management.
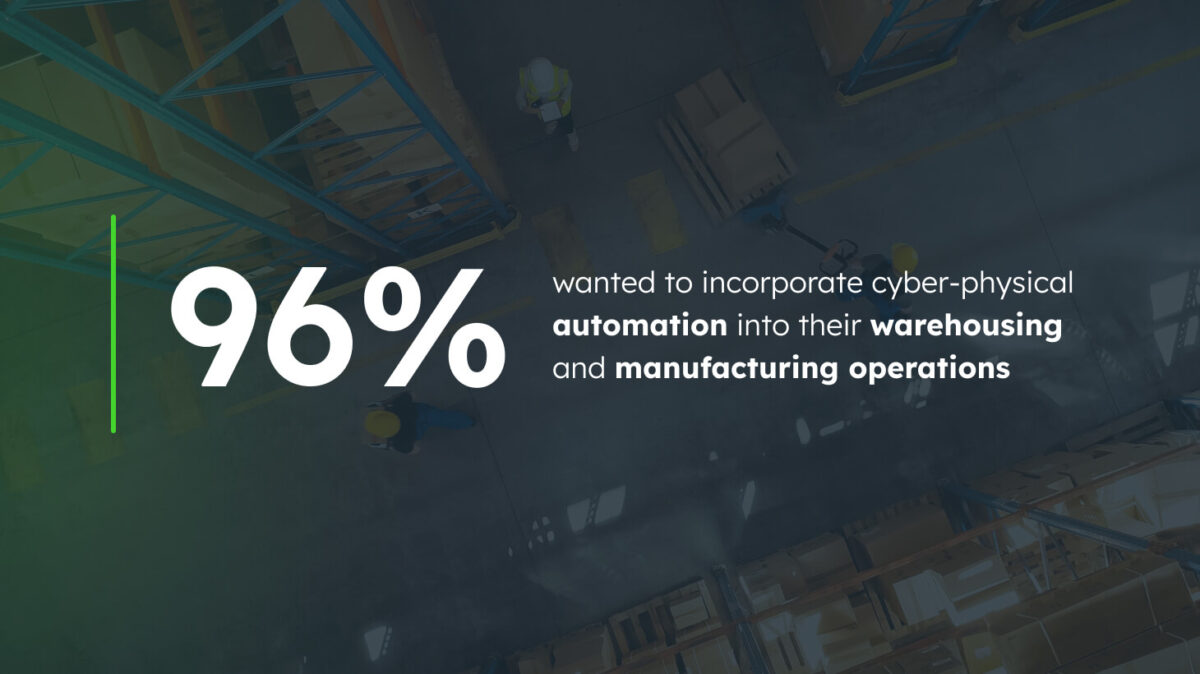
Types of warehouse automation and how it works
The most common types of automation in warehousing today include material handling automation like AGVs and AMRs, storage automation, sortation and distribution automation, and inventory management automation.
Material handling automation: the use of machinery and devices that revolutionize the way materials are transported, handled, stored, and monitored within the warehouse environment. This includes the deployment of conveyor systems that streamline the movement of goods, Automated Guided Vehicles (AGVs) that provide flexible and efficient transport solutions, and robotic palletizers that automate the stacking and organizing of goods onto pallets.
Storage automation: leveraging technology to maximize the storage potential of warehouse facilities. Through the integration of Automated Storage and Retrieval Systems (ASRS), which offer efficient high-density storage solutions, automated stacker cranes that facilitate the storage and retrieval of goods in tall racks, and pallet shuttle systems designed to optimize the storage of palletized goods, warehouses can significantly enhance their storage efficiency.
Picking and packing: this aims to refine the accuracy and speed of the picking and packing phases, critical components of the warehouse operation. Innovations such as goods-to-person systems bring items directly to the packing station, reducing travel time, while pick-to-light systems provide visual cues to streamline the picking process. Robotic picking solutions and automated packaging systems further support these efforts by automating the selection and preparation of goods for shipment.
Sortation and distribution: this type enhances the capability of warehouses to sort and distribute materials swiftly and accurately. This encompasses the use of putwalls, which serve as temporary storage for sorted items, robotic sortation systems that automate the sorting process based on predetermined criteria, and cross-belt sorters that efficiently sort a wide range of items for distribution.
Inventory management: the adoption of technologies aimed at improving the precision and efficiency of inventory control. This includes Warehouse Management Systems (WMS) and Enterprise Resource Planning (ERP) systems that offer comprehensive tools for inventory tracking and management, Radio-Frequency Identification (RFID) technology for real-time inventory tracking, and barcode scanning systems that ensure accurate record-keeping of stock levels.
Key considerations before you start
So where do you begin? In a perfect world, you’d be able to see the path to success before you even take the first step. But, short of that, we can share the key considerations to keep in mind as you plan to leap into warehousing automation.
Simulate, simulate, simulate.
Before you deploy any automation solution, you’ll want to see it in action first. Take advantage of modern simulation and simulate all material workflows, processes, and production configurations. This helps you evaluate whether or not a given solution can perform the way you need it to and will align with expectations, estimated ROI, and required KPIs.
Answering these and other kinds of specific questions through simulation before you head into deployment will not only ensure you’re choosing the right solution for your needs but also save the time and cost of a failed implementation. A failed simulation costs very little, whereas a failed automation project can set you back millions of dollars.
Take a phased approach.
Slow and steady will always win the automation race. Rather than going all in right away with robotics and automation, it’s better to take a more evolutionary approach. Implementing in phases allows you to be more purposeful and responsive to equipment needs and lets you scale your fleet as needs grow.
That’s not to say a fast, “rip and replace” implementation won’t deliver a rapid and solid ROI; it just makes it a bit more tenuous. Plus, it creates the opportunity for miscalculations made at an earlier stage to set you back in your current state and deprives you of things like institutional knowledge held at the worker level that can be lost in a rapid, widespread implementation.
Flexibility is key.
Industry leaders are quickly moving away from large complex systems and leveraging more distributed systems to have the necessary flexibility. For example, most of our customers require multiple robot form factors with varying capabilities. It’s largely why we developed a robust fleet of mobile robots that can handle a range of payloads and weights.
McKinsey proposes three warehouse archetypes that can inform decisions around the design of an automation system. Still, it’s important to remember each warehouse will be different. While you may have similar use cases and repeatable workflows and processes across your business, it’s prudent to consider systems that are appropriate for multiple situations and environments, so you maintain an optimal level of flexibility and reconfigurability.
Get staff onside.
It’s so easy to get caught up in the robot side of automation that you can lose some consideration for the humans working with and alongside them. There are many common misconceptions about robots and autonomous systems that cause people to mistrust their use. The fear of job loss being a main concern.
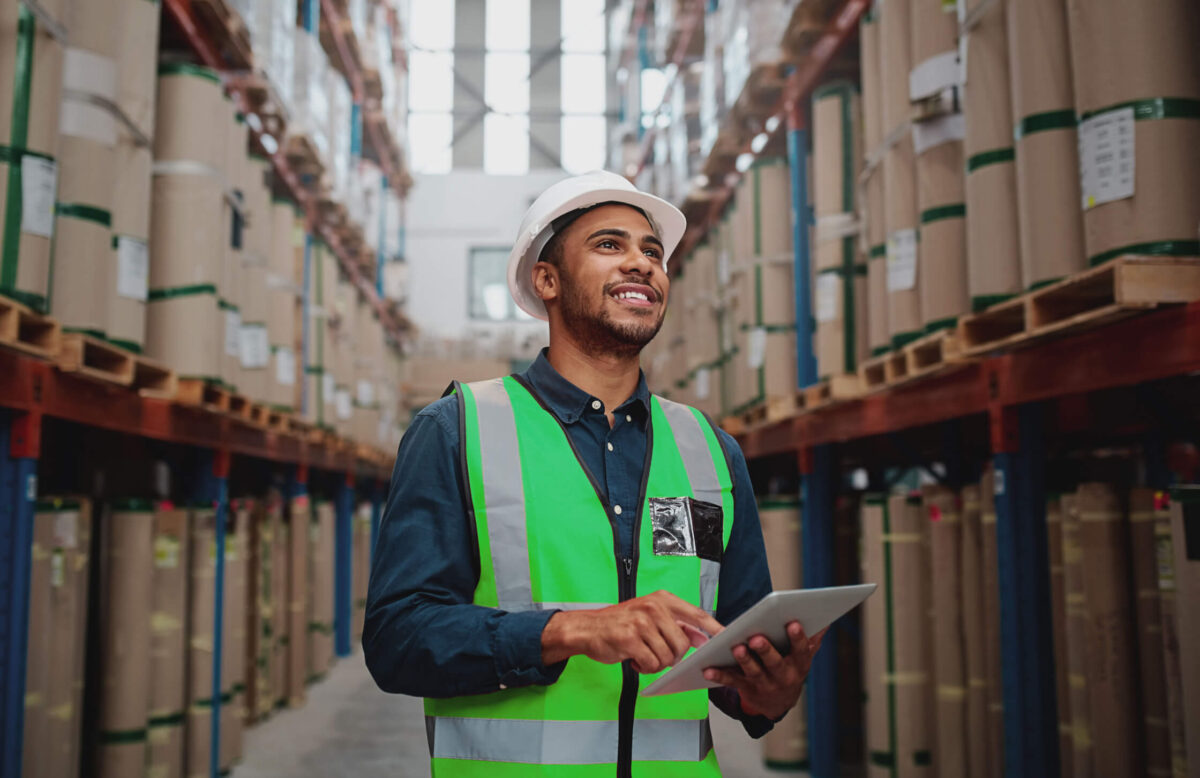
As you develop your implementation strategy, you could create a communication strategy to help eliminate misunderstandings and make the technology accessible to your employees early on. A healthy level of transparency goes a long way in reducing the mystery or resistance to the new autonomous members of the team and, from what we’ve seen, generally leads to much better outcomes.
Taking the time to explain the technology creates a better understanding of the personal and company-wide benefits—allowing your employees to feel involved in the process and see the opportunities available to them within the system.
Support is critical.
If the implementation of an automation solution fails, it’s more often due to weak, post-deployment support and missed or unmet expectations. For this reason, you’ll want to make sure whichever vendor you go with has a robust support program—complete with remote assistance to proactively monitor your fleet of robots and help you address any issues standing in the way of your autonomous solution running smoothly.
This is why our approach to post-deployment support represents a paradigm shift from thinking of robots as a piece of equipment to more of a service. An approach that we (and you should) deem essential to ensure the reliability and safety of your autonomous solution and a way to make sure the investment you make delivers on the value promised.
From No Bot to Robot
One thing is certain about automation in warehousing: there’s no ROI in kicking the tires. Adding to the pressure you feel are the “hidden” costs of labor IDC believes have been undercounted by as much as 50%. While you wait to make your ideal business case for supply chain automation, these costs are adding up.
Our approach to automation is designed to be your release valve. From No Bot to Robot lays out a step-by-step guide to automation in warehousing in 5 easy steps.
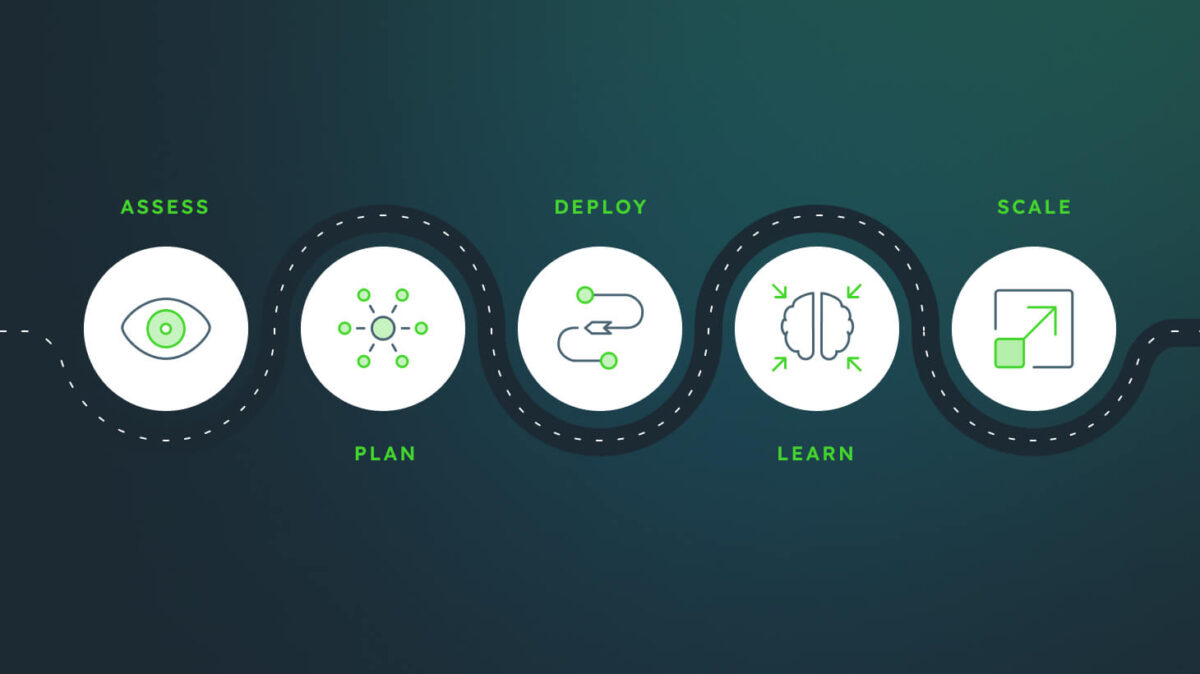
Step 1: Assess
We begin by identifying the pain points within your supply chain network and align that with solutions available on the market—looking at inventory levels, where most of your labor is allocated, and so on.
Based on this understanding, we look for a scalable portion of your network where automation would be most beneficial, define a use case and identify a solution that will result in a solid ROI.
Step 2: Plan
Next, we examine your workflows and choose the appropriate robot type, looking at how the robots interact with the team, facility and systems—determining the number of robots needed for each workflow or route.
We then put your potential robots in real-world environments to ensure they meet expectations, and lastly, we align and define success criteria across stakeholders.
Step 3: Deploy
During the deployment process, we install your robots and onboard and train local staff to ensure they are comfortable using them—helping encourage site adoption and successful operation.
Our six-step deployment process follows a proven roadmap designed to make the deployment phase run as smoothly as possible. We involve customer success teams to help your team and stakeholders understand every aspect.
Step 4: Learn
Throughout the deployment, we involve floor staff and senior management as much as possible, encourage them to ask questions, and schedule multiple training sessions to ensure all staff are adequately trained and comfortable with the robots and the system.
Once the robots are in production and go-live has been achieved, we hand them off to customer success managers who conduct regular check-in meetings with the site—reviewing robot performance metrics and addressing any open topics. Our Pivotal™ command center team (PCC) is also there to provide 24/7/365 support, monitor system performance, and ensure it meets expectations.
Step 5: Scale
Lastly, we work with you to develop a centralized automation strategy to help you decide what to focus on after the initial rollout—using that first site as a launching pad to understand where similar automation can be implemented across your network.
This is also where our Robots as a Service (RaaS) model is beneficial. It not only means you can get the tech you need without a huge upfront capital expense, but it also means you can be responsive to actual equipment needs and increase your fleet when required, all within a low annual fee—giving you the financial flexibility and speed to realize the immediate throughput benefits of your Vecna Robotics automation solution.
The trend toward warehousing automation is catalyzed partly by growing labor shortages, supply chain disruptions, and the widespread preference for direct-to-consumer sales. Three challenges we won’t see let up any time soon.
As you plan for your warehouse automation solution, remember that how a vendor helps you get there is just as crucial as the robots they offer. As we said in the beginning, there is no clear-cut path to success, but knowing what you need and leaning on a vendor with a proven automation adoption roadmap and comprehensive post-deployment support is pretty close.
To learn more about Vecna’s method for implementing warehouse automation, check out our multi-part “From No to Robot” webinar series.
If you’re ready to get started with an initial assessment, contact us to set up an appointment with a Vecna Robotics automation expert.
The Benefits of Warehouse Automation
In the era of digital transformation, industries worldwide are experiencing a seismic shift in operations, and the logistics and supply chain sector is no exception. At the heart of this transformation is warehouse automation. A once labor-intensive operation is now a hub of robotic systems, software applications, and high-tech tools. The benefits of this move towards automation are manifold, reshaping the way businesses handle inventory and order processing.
- Enhanced Efficiency and Productivity: Automated warehouses utilize technology like robots, conveyors, automated storage, and retrieval systems, which can operate around the clock. Unlike human counterparts, machines do not require breaks or shifts. They can consistently operate at optimum levels, thereby increasing the overall output. With systems in place to automatically pick, pack, and transport products, order processing becomes faster and more efficient.
- Cost Savings: While the initial investment in automation might seem high, the long-term ROI is significant. Automation reduces the need for a large workforce, which in turn reduces labor costs. Additionally, automation tends to decrease errors that can arise from manual processes, saving costs associated with reworks, refunds, and compensations.
- Reduced Errors: Human errors, such as mis-picks, mis-ships, or even damaged goods, can be significantly minimized with automation. Systems can be programmed to follow exact specifications, ensuring accuracy in picking and packing processes. Furthermore, integrated software systems can provide real-time inventory tracking, preventing issues related to overstocking or stock-outs.
- Improved Worker Safety: By automating repetitive and potentially dangerous tasks, such as lifting heavy items or operating machinery, the risk of workplace injuries decreases. Robots and automated vehicles can handle these tasks, ensuring that employees are not exposed to undue risks. This not only protects workers but also reduces potential compensation or legal claims.
- Flexibility and Scalability: Automated systems can be designed to be modular and flexible. This means that as a business grows, its automated systems can scale accordingly without the need for a massive overhaul. New modules or robots can be integrated into existing systems, ensuring that businesses can adapt to increasing demands effortlessly.
- Enhanced Data Collection and Analysis: Automation inherently comes with advanced tracking and data collection capabilities. This provides businesses with insights into their operations, enabling them to identify trends, predict demands, and optimize their processes. With a clearer understanding of their operations, businesses can make informed decisions that drive growth.
- Competitive Advantage: In today’s fast-paced market, speed and efficiency are of the essence. Automated warehouses can guarantee quicker order processing and delivery times, giving businesses an edge over competitors. Being able to promise and deliver faster shipments can significantly enhance customer satisfaction and loyalty.
2024 warehouse automation trends and use cases
Here we dive into the cutting-edge technologies and methodologies driving efficiency, accuracy, and flexibility in modern warehousing operations. From AI-driven forecasting to collaborative robotics, discover how these trends are setting new standards for the future of logistics.
Harnessing the power of AI and machine learning: These cutting-edge technologies are revolutionizing warehouses by enabling more precise forecasts and smarter decision-making. By analyzing data patterns, AI and machine learning provide insights for demand forecasting, inventory optimization, and dynamic decision-making, allowing for an agile response to market shifts. Additionally, these technologies empower robots to evolve through interaction with their environment, promoting ongoing enhancements in performance.
Embracing IoT for enhanced efficiency: The proliferation of Internet of Things (IoT) devices is transforming warehouse operations. Through real-time data collection from sensors and devices, IoT technology offers comprehensive monitoring of inventory levels, equipment health, environmental conditions, and workforce productivity. This integration fosters a predictive approach to maintenance and a holistic view of warehouse operations, streamlining processes for heightened efficiency.
Innovating with drones and AMRs: Drones and Autonomous Mobile Robots (AMRs) are setting new standards for operational efficiency in material handling and inventory management. Unlike traditional solutions, AMRs navigate autonomously, adjusting to the warehouse’s dynamic environment. This versatility supports a range of functions, from sorting and picking to transporting goods, thereby improving workflow fluidity and adaptability.
Implementing blockchain for security and transparency: Blockchain technology is becoming indispensable for ensuring transparency and security in warehouse operations. It creates an immutable ledger of transactions, offering real-time tracking of goods and enhancing the visibility of product movements for all stakeholders. Furthermore, blockchain’s inherent security measures play a crucial role in authenticating product legitimacy, particularly critical in combating counterfeit products.
Leveraging VR and AR for training and operations: Virtual Reality (VR) offers immersive training environments, allowing staff to learn procedures and safety protocols in a risk-free setting. Augmented Reality (AR), on the other hand, facilitates remote collaboration and enhances picking processes by overlaying digital information onto the physical world, such as navigational cues and product details. These technologies contribute to a more efficient and interactive warehouse environment.
Adopting flexible automation solutions: The shift towards flexible, modular automation solutions reflects the evolving landscape of e-commerce and customer expectations. Today’s automation technologies, exemplified by Autonomous Mobile Robots (AMRs), are designed to adapt swiftly to changing operational demands, ensuring warehouses can quickly respond to market dynamics without extensive overhauls.
Integrating cobots into workflows: Collaborative robots, or cobots, are redefining efficiency in warehouse settings by working alongside humans to perform repetitive tasks. These advanced machines are not mere tools but partners that work in tandem with human employees, taking on repetitive and physically demanding tasks to free up human workers for more complex, strategic roles. This collaboration is made possible by cobots’ remarkable capacity to learn from their environment and adapt to a wide range of operations, ensuring seamless integration into existing workflows. By doing so, cobots bridge the gap between the flexibility and problem-solving abilities of human workers and the precision, endurance, and consistency of robotic systems. The result is a harmonious blend of human ingenuity and robotic efficiency that not only elevates productivity but also fosters a safer, more engaging work environment.
Advancing with 5G connectivity: The rollout of 5G technology is a game-changer for warehouse automation. This advanced connectivity significantly upgrades the operational backbone of warehouses, enabling the management of enormous data volumes with unmatched velocity. As a result, 5G empowers real-time analytics and decision-making, ensuring automated systems, robotics, and human operators are in constant, fluid communication. This leap in technological capability paves the way for highly integrated, efficient warehouse ecosystems where operational decisions are made in milliseconds, dramatically reducing response times to market demands and operational challenges. The advent of 5G marks the beginning of ultra-responsive, fully interconnected warehouse environments that can adapt swiftly to changing dynamics, setting a new standard in the logistics sector.
These automation use cases not only highlight the versatility and adaptability of modern warehousing solutions but also underscore the potential for significant gains in productivity, accuracy, and operational efficiency. As technology continues to evolve, the scope and impact of warehouse automation are expected to expand further, driving continuous improvement in the logistics and supply chain industry.
A Case for Autonomous Mobile Robots
AMR robots (Autonomous Mobile Robots) are revolutionizing the way warehouses and factories operate, providing operators with the advanced tools they need to meet rising customer expectations and increasingly intensified competition. In an era where speed, efficiency, and accuracy are paramount, an AMR robot is an indispensable asset. These vehicles support a wide range of applications in the modern warehouse and factory, including order picking, inventory management, and resupply requests, functioning as an integrated part of the supply chain process.
With an AMR fleet working alongside human operators on the floor, companies can create a synergistic environment where machines handle repetitive and precision-demanding tasks, and humans focus on more complex, cognitive functions. This collaboration can maximize productivity while reducing errors, allowing employees to concentrate on higher-value tasks that drive real business results. It’s not just about automation for efficiency’s sake; it’s about enhancing the human element of the workforce and creating opportunities for growth, learning, and innovation.
AMRs also represent a flexible and scalable solution, able to adapt to various operational needs and changes in demand. Their ability to integrate with existing systems, and the potential to reprogram them as needs evolve, makes them a future-proof investment. By leveraging this technology, businesses are positioning themselves to be more responsive to market fluctuations and more resilient in the face of unforeseen challenges.
Warehouse automation represents a fundamental transformation in the logistics and supply chain landscape, signaling a move towards more intelligent, responsive, and adaptable operations. This shift is not merely about implementing new technologies; it’s about reimagining the very fabric of warehouse functionality to create systems that are not only more efficient but also more attuned to the needs of workers and the planet.
The adoption of automation technologies such as robotics, AI, and IoT devices is paving the way for warehouses that can predict demand, optimize workflows, and minimize waste on an unprecedented scale. Looking forward, the trajectory of warehouse automation promises not only enhanced operational capabilities but also the potential for creating more sustainable and resilient supply chains. In this era of rapid technological evolution, businesses that invest in understanding and leveraging the full spectrum of automation possibilities will not only thrive but also set new standards for innovation and excellence in the industry.