Automated warehouse robots for material handling have become increasingly vital to distribution and manufacturing leaders as they look to stay ahead of the competition by leveraging new technologies. In exploring the evolving capabilities of intra-logistics robots, you’ll find it is now possible to automate even more processes and reduce time spent on labor-intensive tasks. In this guide, we’ll investigate the types of automated warehouse robots available today and their capabilities to help you to make informed decisions when designing or redesigning your own facility operations. Stay ahead of the competition with the right warehouse automation solutions for your business!
What do automated warehouse robots do?
Material handling warehouse automation robots provide a reliable way to increase the efficiency and safety of warehouse operations. These robots can help with order picking, loading products onto pallets, and transporting them to their designated area. Automated warehouse robots can complete a variety of repetitive tasks, freeing up valuable human resources for higher-level activities. Modern-day warehouse robots come with sophisticated sensors that detect obstacles and prevent accidents or missteps, further enhancing the safety of warehouses. In contrast to previous generations of Automated Guided Vehicles (AGVs) these modern automated systems can not only transport product, but they can also interact with other equipment, thereby requiring less human intervention than ever before.
The advanced navigation system of modern material handling robots signifies a leap towards autonomous operational efficiency, marking a stark departure from the traditional dependency on physical guides. This breakthrough in robotics technology is fueled by sophisticated algorithms and sensors that empower these machines with spatial awareness and real-time decision-making capabilities. The facility map stored within the robot’s memory acts as its internal compass, guiding its movements with precision and reliability, ensuring seamless integration into the dynamic environment of a bustling warehouse.
Unlike their predecessors, these modern Autonomous Mobile Robots (AMRs) are equipped with the intelligence to dynamically navigate through complex warehouse landscapes. This agility allows them to effortlessly maneuver around unexpected obstacles, whether they’re stationary objects or moving personnel, thereby minimizing disruptions to workflow and enhancing overall productivity. The capability to reroute autonomously in response to real-time conditions reflects a significant evolution in warehouse automation, ensuring operations are not just uninterrupted but optimized for speed and efficiency. This adaptability and foresight underline the transformative impact AMRs have on material handling, setting a new benchmark for operational excellence in the logistics and supply chain industry.
The top 10 types of AMRs in use today:
- AGV (Automated Guided Vehicle) robots: These are automated mobile robots that move along predefined paths, guided by magnetic tape, laser targets, or other means. They can be used for repetitive tasks such as transporting goods and materials along fixed routes.
- AMR (Autonomous Mobile Robots): These are advanced AGVs that move freely around the warehouse, adapting routes and operating behaviors as needed. They are very effective for tasks such as picking and transporting goods.
- ASRS (Automated Storage and Retrieval System) robots: These robots are key to inventory management. They move along tracks inside custom structures and are used for storing and retrieving goods in high-density storage areas. They are commonly used in warehouses for storing pallets or other large items.
- Picking robots: These robots are, as the name suggests, specifically designed for picking and packing individual items. They can be equipped with various tools such as grippers, vacuum cups, and cameras to handle different types of products.
- Palletizing robots: These robots are used for stacking and organizing goods on pallets. They can be programmed to handle different sizes and shapes of products, and can be integrated with other warehouse systems such as conveyors and AGVs.
- Sortation robots: These robots are used to sort and route products based on predefined criteria, such as size, weight, or destination. They can be used in conjunction with conveyor systems or mobile robots to automatically sort and route products to their correct locations.
- Inspection robots: These robots are used to inspect and quality check products. They can be equipped with cameras, sensors, and other tools to perform a variety of quality assurance and control tasks.
- Loading and unloading robots: These robots are used to load and unload goods from trucks, shipping containers, and other vehicles. They come in a variety of sizes and can be equipped with various tools such as grippers, vacuum cups, and conveyors to handle different types of products.
- Cleaning robots: These robotic floor scrubbers are used to clean and maintain warehouse facilities. They can be equipped with various tools such as vacuums, mops, and brushes to perform a variety of cleaning tasks.
- Maintenance robots: These robots are used to perform maintenance tasks such as painting, welding, and other repairs. They can be programmed to perform specific tasks and can be integrated with other warehouse systems to perform maintenance tasks automatically.
These robots can help improve efficiency, accuracy, and safety in warehouses, and can help reduce labor costs and increase productivity. However, the implementation of these robots also require significant investments, careful planning and proper integration with existing warehouse systems and processes.
At Vecna Robotics, our focus as a company is to solve your most critical workflows and maximizing throughput by moving your pallets as efficiently as possible with Autonomous Mobile Robots (AMRs). Here is a brief summary the types of pallet-handling robots in our fleet and how they can help your operations right now:
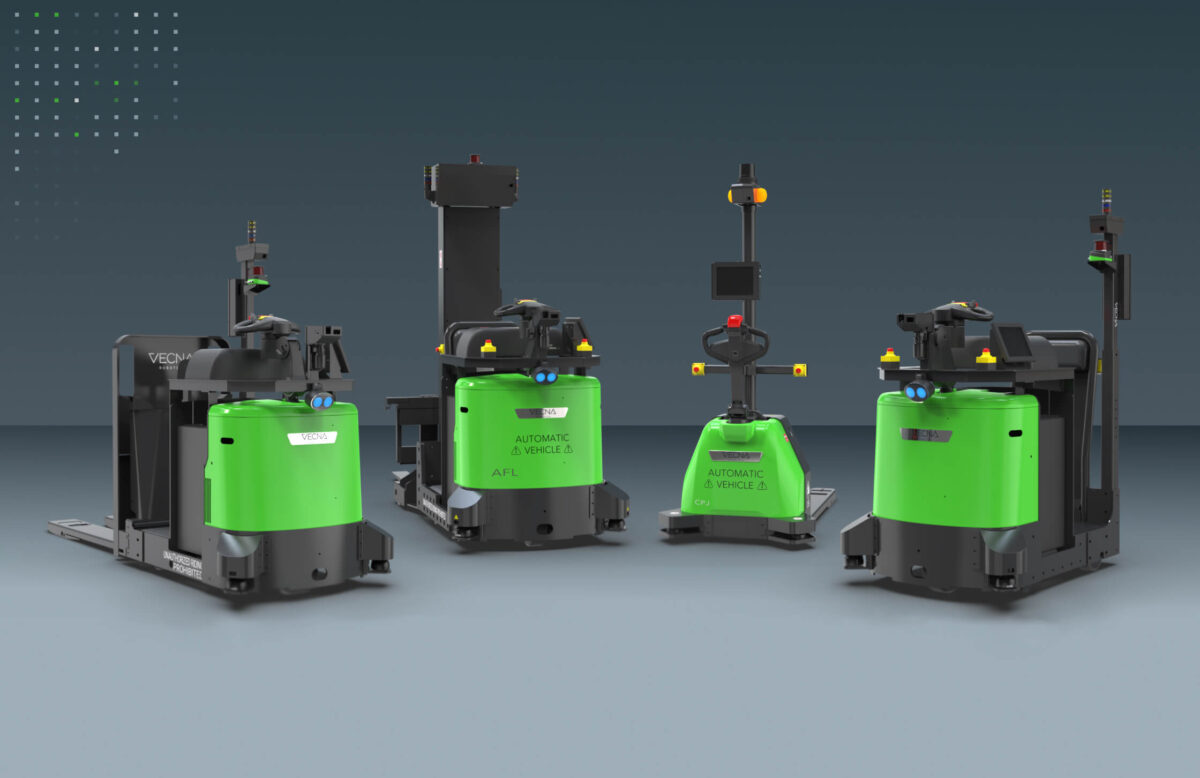
Automated forklifts
Heading up the roster of modern warehouse automation robots is the autonomous forklift. Automated forklifts are essential tools for streamlining warehousing and manufacturing processes. Modern autonomous forklifts transport items with no human driver needed and can also hand off product to other equipment like conveyors, wrapping machines, and pallet stands / racks.
Forklift accidents are notorious, and one common cause is that the driver’s view is obscured by the load. Automated forklifts can always see what’s in front of them and on all sides. They can sense how heavy a load is and won’t attempt to transport a weight that is above their specification. They continuously calculate the maximum speed possible while staying safe – something human operators don’t always do.
The forklift robots can stay in constant wireless communication with a Warehouse Management System (WMS) and be tasked automatically by the WMS. These warehouse robots can also be allocated tasks using a remote tablet or an onboard interface. Best-in-class forklift robots like those from Vecna Robotics have onboard barcode scanners that enable them to verify the pallet they’re moving is the right one.
Autonomous tuggers
When a larger quantity of goods must be moved, an automated tugger can provide the answer. Acting as a locomotive and pulling a “train” of a varying number of carts behind it, the autonomous tugger is a real workhorse. Vecna Robotics metadata from existing customers shows these tuggers reduce the need for material handling personnel by over 50%. The tuggers cut traffic while improving safety and productivity. These automated warehouse robots use dynamic routing that optimizes the path they travel. They can plan the order of their drop-off locations based on real-time availability.
Automated co-bot pallet jack
Collaborative pallet jack robots (co-bots) fill in the gaps for those in-between jobs. Like the manual jack, the co-bot pallet jack is designed for nimble movement in tight spaces. This type of automated warehouse robot is optimized for replenishment, as well as for micro-workflows such as waste/dunnage retrieval, empty pallet transport, tote/cart consolidation, pick-to-packout, and other similar non-value-add tasks. The advanced sensing capabilities of the robot improves safety because it can always see 360 degrees around it, so collisions are avoided. And the physical exertion by workers is minimized, thereby preventing repetitive strain injuries.
Driverless pallet truck
Driverless pallet trucks represent a pinnacle of innovation in warehouse automation, tailored for the heavy-duty transport of goods, including the capability to handle double-stacked pallets weighing up to 8000 lbs. Still considered automated warehouse robots, they shine in their ability to perform extended floor-level hauls, making them indispensable for tasks that demand both power and precision. Ideal for cross-docking, sortation, and critical picking and put-away processes, they redefine efficiency in warehouse operations. Eliminating the need for a driver not only enhances operational speed but also significantly diminishes the potential for human error, contributing to a smoother, more reliable flow of goods. This advancement ensures that warehouses can meet the increasing demands for rapid logistics and supply chain management, setting new benchmarks for efficiency and productivity in the modern market.
The benefits of automated warehouse robots
As businesses seek to advance their competitive edge in the fast-paced world of logistics and supply chain management, the adoption of automated warehouse robots has become a cornerstone for achieving unprecedented levels of operational efficiency and sustainability.
Here, we delve into the multifaceted benefits of integrating these innovative solutions into your warehouse operations, highlighting how they not only streamline processes but also contribute to the broader goals of cost savings, productivity enhancement, and safety improvements.
Sustainability
In an era where environmental concerns are paramount, automated warehouse robots emerge as key players in promoting sustainable operations. By optimizing routes and reducing the need for constant lighting and climate control, these robots significantly lower energy consumption. Their precision and efficiency also minimize waste generation, supporting efforts to achieve green warehousing and supply chain practices. Embracing automated solutions translates to a smaller carbon footprint, aligning your operations with the growing demand for eco-friendly business practices.
Efficiency
The hallmark of automated warehouse robots lies in their ability to redefine efficiency. Through seamless integration with Warehouse Management Systems (WMS), these robots ensure that goods are stored, picked, and transported with unmatched accuracy and speed. The elimination of manual errors and the reduction in time-consuming tasks allow for a smoother flow of operations, ensuring that orders are fulfilled promptly and accurately. This not only boosts throughput but also elevates customer satisfaction, a critical factor in today’s competitive marketplace.
Cost Savings
While the initial investment in automated warehouse technology may seem substantial, the long-term financial benefits are undeniable. By automating repetitive and labor-intensive tasks, businesses can significantly reduce labor costs and dependency on a large workforce. Additionally, the enhanced accuracy and reduced waste contribute to cost savings, minimizing losses from damaged goods and inefficiencies. Automated systems are designed for scalability, allowing businesses to adjust their operations to meet demand without the proportional increase in costs associated with traditional labor.
Productivity and Safety
The integration of automated robots in warehouse operations goes hand in hand with improvements in productivity and workplace safety. Robots can operate around the clock, providing a continuous output that human workers cannot match. This relentless productivity ensures that businesses can meet increasing demands without compromising on delivery times or service quality.
Safety, a paramount concern in any warehouse environment, is significantly enhanced through automation. Robots are designed to handle heavy lifting and navigate busy warehouse floors with precision, reducing the risk of workplace injuries associated with manual labor. Their advanced sensing technologies prevent accidents, creating a safer working environment for all employees.
By harnessing the power of automated warehouse robots, businesses can achieve a harmonious balance between operational efficiency, cost-effectiveness, environmental sustainability, and employee welfare. As the landscape of logistics and supply chain management continues to evolve, staying ahead of the curve with advanced automation solutions will ensure that your operations are not only efficient and sustainable but also primed for future growth and success.
Addressing the labor shortage
In the face of pervasive labor shortages plaguing industries worldwide, automated warehouse robots emerge as a pivotal solution, elegantly bridging the gap between demand and workforce availability. These sophisticated robots, designed with precision and efficiency in mind, assume the mantle of repetitive, labor-intensive tasks, ensuring warehouses remain operable and productive even when human resources are scarce. By automating core processes, these robotic systems not only alleviate the strain on existing staff but also redefine productivity benchmarks. The seamless integration of automated robots into warehouse operations underscores a strategic response to labor shortages, enabling businesses to sustain growth and competitiveness without being tethered to the constraints of the labor market.
Automated warehouse robots not only address the immediate issue of filling labor gaps but also offer a long-term strategy for enhancing workflow and reducing dependence on a fluctuating labor market. Their deployment allows warehouses to maintain continuous operations, optimize resource allocation, and future-proof against workforce uncertainties. By embracing these automated solutions, companies can navigate the complexities of labor shortages with confidence, ensuring resilience and sustained operational excellence in an ever-evolving industrial landscape.
The business case for warehouse automation
In an era where time is synonymous with cost, the imperative to streamline warehousing processes has never been more critical. The burgeoning e-commerce sector, along with the escalating expectations for rapid delivery, compels warehouses to embrace the next wave of technological innovation. Automated forklifts, autonomous tuggers, automated co-bot pallet jacks, and driverless pallet trucks represent the forefront of this revolution. These cutting-edge solutions not only bolster the precision and reliability of warehouse operations but also significantly mitigate the risks associated with manual handling and maneuvering in densely packed environments. By integrating these advanced robotics into their core operations, warehouses are not just meeting the modern demands for speed and efficiency; they are setting new standards for operational excellence. This transition to automated systems marks a pivotal shift towards creating smarter, safer, and more sustainable warehouse ecosystems, ensuring businesses remain competitive in the fast-paced global market.
Embracing the new era of warehouse automation might seem daunting due to its novelty and the perceived complexities involved. However, it’s essential to recognize that with thoughtful planning, clear objectives, and the collaboration of experienced technology partners, the transition to automation can be streamlined and rewarding. Adopting these advanced systems enhances operational efficiency and opens up avenues for scalability and innovation, setting a solid foundation for future growth. Let expertise and strategic partnership guide you through the process, making it a valuable investment in your operational evolution.
Need to know more? Reach out to a friendly and knowledgeable Vecna Robotics representative who can help you navigate your unique automation journey.